Rabu, 30 Juli 2008
Senin, 28 Juli 2008
Hard Disk (HDD)
Hard disk adalah suatu device dari PC yang berfungsi sebagai media penyimpan data (storage) dan juga termasuk ke dalam salah satu memori eksternal dari sebuah PC.
Hard disk sendiri terdiri dari berbagai komponen - komponen pembentuk hard disk dan akan dijelaskan di bawah ini.
FAT
File system yang digunakan oleh DOS dan Windows 9x/ME. FAT (File Allocation Table) terdiri dari FAT12(12bit), FAT16(16bit), dan FAT32(32bit). Batas max dalam satu file yang bias di simpan ini bervariasi FAT12=32MB, FAT16=2GB dan FAT32=4GB, sedangkan untuk batas max harddisk yang bias dikenali adalah 2 TBuntuk FAT32. Untuk saat ini versi FAT yang masih sering digunakan adalah FAT32 yakni pada Windows 9X/ME.
NTFS
New Technology File System adalah standar file system yang digunakan oleh windows NT dan variannya seperti Windows 2000, Windows XP, Windows 2003 dan Windows Vistal berbeda dengan FAT, NTFS tdk bekerja dengan cluster table namun menggunakan MFT(Master File Table)
MBR
Sektor dari sebuah partisi yang ada dalam harddisk dan menempati sector pertama dari harddisk tsb. Sector pertama yang di tempati oleh MBR adalah sebesar 512 byte dan berisikan bootloader supaya harddisk tsb bias melakukan booting OS( Operating System : Windows) atau sekedar dikenali oleh system. Dalam satu MBR bias dijadikan empat buah primary partition dan sebuah extended partition
Cluster
Dalam beberapa file system seperti FAT dan NTFS, cluster adalah bagian dari kapasitas diskyang di alokasikan untuk direktori file. Cluster terdiri dari sekumpulan sector, di mana satu sector berkapasitas 512 byte.
Extended Partition
Di dalam MBR (Master Boot Sektor) hanya satu partisi yang bias dijadikan extended partition. Dimana extended partition memerlukan 512 byte dari sebuah partisi Extended Partition ini oleh system akan di sebut dengan logical drive sehingga secara otomatis ia berada di luar MBR.
Capacity
Merupakan besar maksimal daya tampung data di dalam harddisk, yang biasanya di ukur dalam satuan Byte.
KOMPONEN - KOMPONEN PADA HARDDISK
Piringan logam
Piringan logam (platter) yang berfungsi sebagai tempat penyimpan data. Jumlah piringan ini beragam, mulai 1, 2,3 atau lebih.
Piringan ini diberi lapisan bahan magnetis yang sangat-sangat tipis (ketebalan dalam orde per sejuta inchi).
Pada saat ini digunakan teknologi thin film (seperti pada prosesor) untuk membuat lapisan tersebut.
Head (berupa kumparan)
Head pada hard disk berbeda dengan head pada tape. Pada tape proses baca dan tulis (rekam) menggunakan dua head yang berbeda, sedangkan pada hard disk proses baca dan tulis menggunakan head yang sama. HD biasanya memiliki head untuk tiap-tiap sisi platter, untuk hard disk dengan 2 platter dapat memiliki sampai 4 head, hard disk dengan 3 platter dapat memiliki sampai 6 platter. Tetapi tidak berarti hardisk dengan 16 head harus memiliki 8 platter. Di sinilah kita kenal teknik translasi. Rangkaian Elektronik pada PCB (printed circuit board) , terdiri dari:
Read Preamplifier
Rangkaian penguat untuk pembacaan (read preamplifier) yang diperlukan karena signal yang diperoleh head dari piringan sangat lemah.
DSP (digital signal processor), untuk proses yang berhubungan dengan sinyal-sinyal digital, seperti konversi sinyal listrik yang datang menjadi sinyal digital yang akan dituliskan ke piringan.
Chip Memory
Dipergunakan sebagai cache buffer
Konektor
Untuk melakukan komunikasi dengan CPU. Untuk HD IDE, jumlahnya 40 pin
Spindle dan actuator arm motor controller, untuk mengontrol putaran piringan dan peletakkan head baca/tulis.
Motor dari hard disk berfungsi untuk memutar platter. Ketika komputer distart, motor ini mulai bekerja dan memperdengarkan suara yang khas. Jika suara ini tidak benar maka dapat diduga bahwa motor HD tidak bekerja dengan baik.
Kecepatan putar motor ini mulai dari 3600 rpm sampai 10000 rpm dengan arah berlawanan dengan arah perputaran jarum jam (counter-clockwise). Putaran yang sangat cepat ini mengakibatkan adanya gaya pada permukaan piringan yang disebabkan oleh udara. Gaya ini memungkinkan head untuk mengambang pada ketinggian beberapa mikro inchi di atas permukaan platter/piringan. di atas piringan. Drive semacam ini disebut bernoulli drive. "Ketinggian" ini jauh lebih kecil dibanding ukuran rambut manusia, apalagi debu dari rokok.
Jarak yang dekat ini dimaksudkan agar head dapat membaca atau menulis dengan kerapatan yang tinggi. Dengan jarak sedekat itu, Anda tidak perlu terlalu takut. Hard disk sudah dirancang agar dalam keadaan normal (harap diingat) head tidak menyentuh permukaan platter. Jika hard disk dimatikan, maka piringan akan berhenti berputar akibatnya gaya yang mengangkat head akan hilang dan head akan mendarat di piringan.
Lokasi pendaratan head sudah ditentukan pada daerah tertentu yang disebut landing zone (LZone) sehingga tidak akan merusak data yang ada pada daerah lain.
Jika dalam keadaan bekerja head sedikit saja tergoncang, maka akan menyebabkan head akan menyentuh permukaan piringan dan kemungkinan besar akan menyebabkan kehilangan data, kerusakan sebagian kecil dari piringan akan merusak head atau seluruh piringan.
Bayangkan jika pada saat tertempel pada piringan akibat ada goncangan ada perintah bergerak ke tempat lain, maka head akan meninggalkan "jejak-jejak" bad sector pada piringan hard disk. Tapi pembuat hard disk sudah merancang agar head tetap stabil dalam kondisi goncangan tertentu, saat ini goncangan yang dapat ditoleransi mencapai 70 sampai 100 kali gravitasi (70-100 G).
HEAD
Adalah komponen yang paling mahal dari hard disk dan karakteristik head sangat menentukan kinerja hard disk. Head terbuat dari bahan magnetis dengan bentuk seperti "C". Kumparan (koil) yang terbuat dari kawat mengelilingi head. Pada saat menulis, arus yang melewati koil akan menimbulkan medan magnet yang digunakan untuk memagnetisasi permukaan platter. Sedangkan pada saat membaca, medan magnet pada permukaan platter akan menimbulkan arus pada koil ini.
Data "0" dan "1" disimpan dalam piringan dalam bentuk pola-pola magnet. Head baca/tulis membentuk pola ini ke piringan ketika proses penulisan terjadi, ketika membaca head akan mengkonversi bentuk pola ini ke dalam bentuk "0" dan "1". Lapisan magnetik terdiri dari daerah-daerah mikroskopik yang disebut domain. Setiap domain seperti magnet mungil dengan kutub-kutub yang berlawanan (utara/selatan atau positif/negatif). Data "1" dipresentasikan sebagai daerah dengan kutub positif di sisi kiri sedangkan data "0" dipresentasikan sebagai daerah dengan kutub positif di sisi kanan. Ada cara efektif untuk merekam data "0" dan "1" yaitu dengan teknik flux reversal. Ketika head akan menuliskan "1" maka head akan membalik polaritas magnet, sedangkan untuk "0" head tidak akan membalik polaritasnya.
Gerakan head dikendalikan oleh actuator arm (lengan penggerak). Kombinasi dari head dan platter sering disebut head disk assembly (HDA). Actuator arm digerakkan oleh positioning motor, yaitu motor yang berfungsi untuk mengatur posisi dari lengan (dan tentu saja posisi dari head). Motor ini dikontrol oleh hard disk controller pada rangkaian elektronik di hard disk. Motor ini memiliki sistem kontrol yang amat hebat, dengan sistem feedback motor ini dapat meletakkan head baca/tulis pada posisi yang sangat akurat. Mengapa hal ini dapat dilakukan? Vendor hard disk menggunakan suatu teknik yang disebut servo positioning, teknik inilah yang memungkinkan adanya feedback dalam sistem kontrol penempatan head hard disk.
Servo sendiri berisi informasi mengenai track dsb yang sangat penting dalam proses penempatan head.
Teknik ini memiliki dua tipe, yaitu
* dedicated servo dan
* embedded servo.
Dedicated servo menggunakan satu permukaan dari hard disk hanya untuk servo saja. Tentu saja cara ini merugikan karena menghabiskan tempat pada hard disk. Teknik kedua (embedded servo) menempatkan informasi servo secara tersebar pada setiap track sehingga kapasitas hard disk tetap dapat dipertahankan. Pada kenyataannya, saat ini teknik kedua yang digunakan, sedangkan teknik pertama digunakan pada hard disk yang dibuat pada masa lalu.
Tenkyu Broder.... Tjetjep
Hard disk sendiri terdiri dari berbagai komponen - komponen pembentuk hard disk dan akan dijelaskan di bawah ini.
FAT
File system yang digunakan oleh DOS dan Windows 9x/ME. FAT (File Allocation Table) terdiri dari FAT12(12bit), FAT16(16bit), dan FAT32(32bit). Batas max dalam satu file yang bias di simpan ini bervariasi FAT12=32MB, FAT16=2GB dan FAT32=4GB, sedangkan untuk batas max harddisk yang bias dikenali adalah 2 TBuntuk FAT32. Untuk saat ini versi FAT yang masih sering digunakan adalah FAT32 yakni pada Windows 9X/ME.
NTFS
New Technology File System adalah standar file system yang digunakan oleh windows NT dan variannya seperti Windows 2000, Windows XP, Windows 2003 dan Windows Vistal berbeda dengan FAT, NTFS tdk bekerja dengan cluster table namun menggunakan MFT(Master File Table)
MBR
Sektor dari sebuah partisi yang ada dalam harddisk dan menempati sector pertama dari harddisk tsb. Sector pertama yang di tempati oleh MBR adalah sebesar 512 byte dan berisikan bootloader supaya harddisk tsb bias melakukan booting OS( Operating System : Windows) atau sekedar dikenali oleh system. Dalam satu MBR bias dijadikan empat buah primary partition dan sebuah extended partition
Cluster
Dalam beberapa file system seperti FAT dan NTFS, cluster adalah bagian dari kapasitas diskyang di alokasikan untuk direktori file. Cluster terdiri dari sekumpulan sector, di mana satu sector berkapasitas 512 byte.
Extended Partition
Di dalam MBR (Master Boot Sektor) hanya satu partisi yang bias dijadikan extended partition. Dimana extended partition memerlukan 512 byte dari sebuah partisi Extended Partition ini oleh system akan di sebut dengan logical drive sehingga secara otomatis ia berada di luar MBR.
Capacity
Merupakan besar maksimal daya tampung data di dalam harddisk, yang biasanya di ukur dalam satuan Byte.
KOMPONEN - KOMPONEN PADA HARDDISK
Piringan logam
Piringan logam (platter) yang berfungsi sebagai tempat penyimpan data. Jumlah piringan ini beragam, mulai 1, 2,3 atau lebih.
Piringan ini diberi lapisan bahan magnetis yang sangat-sangat tipis (ketebalan dalam orde per sejuta inchi).
Pada saat ini digunakan teknologi thin film (seperti pada prosesor) untuk membuat lapisan tersebut.
Head (berupa kumparan)
Head pada hard disk berbeda dengan head pada tape. Pada tape proses baca dan tulis (rekam) menggunakan dua head yang berbeda, sedangkan pada hard disk proses baca dan tulis menggunakan head yang sama. HD biasanya memiliki head untuk tiap-tiap sisi platter, untuk hard disk dengan 2 platter dapat memiliki sampai 4 head, hard disk dengan 3 platter dapat memiliki sampai 6 platter. Tetapi tidak berarti hardisk dengan 16 head harus memiliki 8 platter. Di sinilah kita kenal teknik translasi. Rangkaian Elektronik pada PCB (printed circuit board) , terdiri dari:
Read Preamplifier
Rangkaian penguat untuk pembacaan (read preamplifier) yang diperlukan karena signal yang diperoleh head dari piringan sangat lemah.
DSP (digital signal processor), untuk proses yang berhubungan dengan sinyal-sinyal digital, seperti konversi sinyal listrik yang datang menjadi sinyal digital yang akan dituliskan ke piringan.
Chip Memory
Dipergunakan sebagai cache buffer
Konektor
Untuk melakukan komunikasi dengan CPU. Untuk HD IDE, jumlahnya 40 pin
Spindle dan actuator arm motor controller, untuk mengontrol putaran piringan dan peletakkan head baca/tulis.
Motor dari hard disk berfungsi untuk memutar platter. Ketika komputer distart, motor ini mulai bekerja dan memperdengarkan suara yang khas. Jika suara ini tidak benar maka dapat diduga bahwa motor HD tidak bekerja dengan baik.
Kecepatan putar motor ini mulai dari 3600 rpm sampai 10000 rpm dengan arah berlawanan dengan arah perputaran jarum jam (counter-clockwise). Putaran yang sangat cepat ini mengakibatkan adanya gaya pada permukaan piringan yang disebabkan oleh udara. Gaya ini memungkinkan head untuk mengambang pada ketinggian beberapa mikro inchi di atas permukaan platter/piringan. di atas piringan. Drive semacam ini disebut bernoulli drive. "Ketinggian" ini jauh lebih kecil dibanding ukuran rambut manusia, apalagi debu dari rokok.
Jarak yang dekat ini dimaksudkan agar head dapat membaca atau menulis dengan kerapatan yang tinggi. Dengan jarak sedekat itu, Anda tidak perlu terlalu takut. Hard disk sudah dirancang agar dalam keadaan normal (harap diingat) head tidak menyentuh permukaan platter. Jika hard disk dimatikan, maka piringan akan berhenti berputar akibatnya gaya yang mengangkat head akan hilang dan head akan mendarat di piringan.
Lokasi pendaratan head sudah ditentukan pada daerah tertentu yang disebut landing zone (LZone) sehingga tidak akan merusak data yang ada pada daerah lain.
Jika dalam keadaan bekerja head sedikit saja tergoncang, maka akan menyebabkan head akan menyentuh permukaan piringan dan kemungkinan besar akan menyebabkan kehilangan data, kerusakan sebagian kecil dari piringan akan merusak head atau seluruh piringan.
Bayangkan jika pada saat tertempel pada piringan akibat ada goncangan ada perintah bergerak ke tempat lain, maka head akan meninggalkan "jejak-jejak" bad sector pada piringan hard disk. Tapi pembuat hard disk sudah merancang agar head tetap stabil dalam kondisi goncangan tertentu, saat ini goncangan yang dapat ditoleransi mencapai 70 sampai 100 kali gravitasi (70-100 G).
HEAD
Adalah komponen yang paling mahal dari hard disk dan karakteristik head sangat menentukan kinerja hard disk. Head terbuat dari bahan magnetis dengan bentuk seperti "C". Kumparan (koil) yang terbuat dari kawat mengelilingi head. Pada saat menulis, arus yang melewati koil akan menimbulkan medan magnet yang digunakan untuk memagnetisasi permukaan platter. Sedangkan pada saat membaca, medan magnet pada permukaan platter akan menimbulkan arus pada koil ini.
Data "0" dan "1" disimpan dalam piringan dalam bentuk pola-pola magnet. Head baca/tulis membentuk pola ini ke piringan ketika proses penulisan terjadi, ketika membaca head akan mengkonversi bentuk pola ini ke dalam bentuk "0" dan "1". Lapisan magnetik terdiri dari daerah-daerah mikroskopik yang disebut domain. Setiap domain seperti magnet mungil dengan kutub-kutub yang berlawanan (utara/selatan atau positif/negatif). Data "1" dipresentasikan sebagai daerah dengan kutub positif di sisi kiri sedangkan data "0" dipresentasikan sebagai daerah dengan kutub positif di sisi kanan. Ada cara efektif untuk merekam data "0" dan "1" yaitu dengan teknik flux reversal. Ketika head akan menuliskan "1" maka head akan membalik polaritas magnet, sedangkan untuk "0" head tidak akan membalik polaritasnya.
Gerakan head dikendalikan oleh actuator arm (lengan penggerak). Kombinasi dari head dan platter sering disebut head disk assembly (HDA). Actuator arm digerakkan oleh positioning motor, yaitu motor yang berfungsi untuk mengatur posisi dari lengan (dan tentu saja posisi dari head). Motor ini dikontrol oleh hard disk controller pada rangkaian elektronik di hard disk. Motor ini memiliki sistem kontrol yang amat hebat, dengan sistem feedback motor ini dapat meletakkan head baca/tulis pada posisi yang sangat akurat. Mengapa hal ini dapat dilakukan? Vendor hard disk menggunakan suatu teknik yang disebut servo positioning, teknik inilah yang memungkinkan adanya feedback dalam sistem kontrol penempatan head hard disk.
Servo sendiri berisi informasi mengenai track dsb yang sangat penting dalam proses penempatan head.
Teknik ini memiliki dua tipe, yaitu
* dedicated servo dan
* embedded servo.
Dedicated servo menggunakan satu permukaan dari hard disk hanya untuk servo saja. Tentu saja cara ini merugikan karena menghabiskan tempat pada hard disk. Teknik kedua (embedded servo) menempatkan informasi servo secara tersebar pada setiap track sehingga kapasitas hard disk tetap dapat dipertahankan. Pada kenyataannya, saat ini teknik kedua yang digunakan, sedangkan teknik pertama digunakan pada hard disk yang dibuat pada masa lalu.
Tenkyu Broder.... Tjetjep
Merawat Flashdisk
Jangan Terkena Air
Meski ada beberapa merk yang mengklaim waterproof, menjauhkan flash disk dari sentuhan air tetap saja menjadi langkah yang paling aman. Daripada data kamu hilang, mendingan tidak ambil resiko kan?
Tidak Terkena Suhu Udara Panas
Semua barang elektronik tak terkecuali flash disk sangat rentan dengan yang namanya panas. Apalagi terkena sinar matahari langsung. Jadi usahakan tidak menyimpannya ditempat yang panas dan terkena sinar matahari langsung. Misalnya seperti meninggalkan flash disk di dashboard mobil.
Meminimalisir Proses Write and Copy Paste File
Artinya suatu saat flash disk kita bisa mati dan tidak bisa digunakan lagi. Usia flash disk berbeda-beda, tergantung kualitas dan merk dari flash disk itu sendiri. Biasanya usia flash disk antara 10.000-100.000 kali proses hapus tulis. Jadi usahakan untuk meminimalisir proses tersebut dan juga mengedit langsung dari flash disk
Jauhkan Dari Medan Magnet
Barang-barang elektronik seperti tv dan handphone sangat tidak baik untuk flash disk. Untuk itu jangan pernah menyimpannya di dekat barang-barang sejenis yang memiliki kekuatan magnet besar. Terkadang kita sering lupa jika meletakkan flash disk dan hand phone di tempat sama dalam tas. Nah mulai saat ini, kalau pingin flash disk kamu berumur panjang, jangan lagi menyimpannya di tempat sama ya?!
Hindari Benturan Keras
Janganlah flash disk di jatuhkan dari lantai yang tinggi ke lantai dasar yang keras ataupun dilemparkan benda keras lainnya.
Selalu Melakukan Pengecekan Virus Dengan Anti Virus
Saat Pengambilan data atau pemindahan dari dari pc ke flash disk, sangat mungkin bukan hanya data yang ikut berpindah tapi juga virus-virus yang terdapat dalam komputer. Apalagi kalau kita mengambil dan menyimpan data dari internet. Waduh flash disk kamu bisa dipenuhi virus-virus pengganggu. Makanya, jangan lupa untuk melakukan ritual scan virus secara berkala dengan software anti virus yang tersedia.
Proses Eject atau Stop
Selalu melakukan proses eject atau stop sebelum mencabut flash disk dari port usb. Selain bisa menjadikan flash disk rusak, tidak melakukan proses eject atau stop juga dapat mempengaruhi file-file data yang di simpan di dalamnya.
Flash Disk Harus Selalu Dalam Keadaan Tertutup Jika Tidak Dipergunakan
Udara dan lingkungan kita penuh dengan debu dan kotoran. Jika socket flash disk kita kotor maka dapat mengakibatkan proses baca tulis sering gagal.
Meski ada beberapa merk yang mengklaim waterproof, menjauhkan flash disk dari sentuhan air tetap saja menjadi langkah yang paling aman. Daripada data kamu hilang, mendingan tidak ambil resiko kan?
Tidak Terkena Suhu Udara Panas
Semua barang elektronik tak terkecuali flash disk sangat rentan dengan yang namanya panas. Apalagi terkena sinar matahari langsung. Jadi usahakan tidak menyimpannya ditempat yang panas dan terkena sinar matahari langsung. Misalnya seperti meninggalkan flash disk di dashboard mobil.
Meminimalisir Proses Write and Copy Paste File
Artinya suatu saat flash disk kita bisa mati dan tidak bisa digunakan lagi. Usia flash disk berbeda-beda, tergantung kualitas dan merk dari flash disk itu sendiri. Biasanya usia flash disk antara 10.000-100.000 kali proses hapus tulis. Jadi usahakan untuk meminimalisir proses tersebut dan juga mengedit langsung dari flash disk
Jauhkan Dari Medan Magnet
Barang-barang elektronik seperti tv dan handphone sangat tidak baik untuk flash disk. Untuk itu jangan pernah menyimpannya di dekat barang-barang sejenis yang memiliki kekuatan magnet besar. Terkadang kita sering lupa jika meletakkan flash disk dan hand phone di tempat sama dalam tas. Nah mulai saat ini, kalau pingin flash disk kamu berumur panjang, jangan lagi menyimpannya di tempat sama ya?!
Hindari Benturan Keras
Janganlah flash disk di jatuhkan dari lantai yang tinggi ke lantai dasar yang keras ataupun dilemparkan benda keras lainnya.
Selalu Melakukan Pengecekan Virus Dengan Anti Virus
Saat Pengambilan data atau pemindahan dari dari pc ke flash disk, sangat mungkin bukan hanya data yang ikut berpindah tapi juga virus-virus yang terdapat dalam komputer. Apalagi kalau kita mengambil dan menyimpan data dari internet. Waduh flash disk kamu bisa dipenuhi virus-virus pengganggu. Makanya, jangan lupa untuk melakukan ritual scan virus secara berkala dengan software anti virus yang tersedia.
Proses Eject atau Stop
Selalu melakukan proses eject atau stop sebelum mencabut flash disk dari port usb. Selain bisa menjadikan flash disk rusak, tidak melakukan proses eject atau stop juga dapat mempengaruhi file-file data yang di simpan di dalamnya.
Flash Disk Harus Selalu Dalam Keadaan Tertutup Jika Tidak Dipergunakan
Udara dan lingkungan kita penuh dengan debu dan kotoran. Jika socket flash disk kita kotor maka dapat mengakibatkan proses baca tulis sering gagal.
ELECTRICAL SAFETY AND ELECTRICAL DEFINITIONS
The danger of injury through electrical shock is possible whenever electrical power is
present. When a person's body completes a circuit and thus connects a power source
with the ground, an electrical burn or injury is imminent. Most fatal injuries result from high-voltage exposure; however, people can sustain severe injuries from low voltage power if it has a high current flow.
Electrical safety is important in every work environment. The following sections cover circuit breaker loads, electrical grounding, electrical safety guidelines, and electrical emergency response.
Electrical Definitions
The following definitions help clarify general electrical safety:
* Amps: the standard unit for measuring electrical current.
* Watt: a unit of electrical power, equal to the power developed in a circuit by a
current of amp flowing through a potential difference of one volt.
* Voltage: electromotive force expressed in volts.
* Circuit Breaker: a device that automatically interrupts the flow of an electrical
current.
* Breaker Box: an insulated box on which interconnected circuits are mounted.
* Electrical Panel: an insulated panel on which electrical wires are mounted.
* Current Flow: the rate of flow of an electrical charge, generally expressed in amps.
* Electrical Load: the amount of power delivered by a generator or carried by a circuit. A device to which the power is delivered.
* Ground-Fault Circuit Interrupter (GFCI): a GFCI detects grounding problems
and shuts electricity off to prevent a possible accident.
* High Voltage: the term high voltage applies to electrical equipment that operates at
more than 600 Volts (for terminal to terminal operation) or more than 300 Volts (for
terminal to ground operation). Low voltage, high current AC or DC power supplies
are also considered to be high voltage.
* Hazardous Energy Sources: this term applies to stored or residual energy such as
that in capacitors, springs, elevated machine members, rotating flywheels, hydraulic
systems, and air, gas, steam, or water pressure
* Lockout: the placement of a lock on an energy-isolating device. This act prevents
workers from operating a piece of equipment until the lock is removed.
* Tagout: the placement of a tag on an energy-isolating device. A tagout device is a
prominent warning device of a lockout.
Energy-Isolating Device: a mechanical device that prevents the transmission or
release of energy.
Examples include the following:
* Manually operated circuit breakers
* Disconnect switches
* Line or block valves
Pushbuttons, selector switches, and other control circuit devices do not isolate energy. Energy-isolating devices should be lockable by means of a hasp or other type of attachment. It should not be necessary to dismantle or reassemble a device to lock it.
Authorized Employee: a person who locks out or tags out equipment for
service or maintenance. Authorized employees have been formally trained in
proper lockout/tagout procedures.
Electrical Safety : Circuit Breaker Loads
Most office and laboratory locations have 20 amp circuit breakers that serve two or
more outlets. These breakers can handle most office equipment; however, the widespread use of personal computers and associated hardware can create an electrical overload. To determine your current electrical load, follow these steps:
1. Check office/laboratory equipment for a manufacturer's rating label that indicates total watts or amps. Take special care to check appliances that use electricity to generate heat.
2. Convert the watts rating to amps: Amps = Watts ÷ 120 Volts
3. Total the amps for each circuit.
4. If the total equals more than 15 amps per 20 amp circuit, you may overloading the circuit. Move enough equipment to a different circuit to reduce the circuit load; otherwise, have the Physical Plant inspect the circuit wiring.
Electrical Safety: Electrical Grounding
Proper electrical grounding can help prevent electrical injury. Most electrical equipment is grounded with either a three-prong plug or a two-prong plug and
insulation. Because a grounding system may be defective without your knowledge,
use a GFCI to ensure electrical safety. GFCIs are required in moist or potentially damp environments.
Electrical Safety: Electrical Panels
Electrical panels or breaker boxes require special safety considerations, including the following:
* Know where your panel box is located.
* Do not tape circuit switches to keep a breaker from tripping.
* Ensure that breaker circuits are accurately labeled within panel boxes.
* Ensure that panel box doors are securely attached.
* Do not block panel boxes. There should be at least 36 inches of clear space in front of a panel box.
Report, tripped breakers and refer any electrical questions to the Physical Plant.
Electrical Safety : Guidelines
Follow these guidelines for general electrical safety:
* Be familiar with the electrical hazards associated with your workplace.
* Unplug electrical equipment before repairing or servicing it.
* If a prong breaks off inside an outlet, do not attempt to remove it yourself. Call the Physical Plant for assistance.
* Ensure that outlets are firmly mounted. Report loose outlets to the Physical Plant.
* Report all electrical problems, including tripped breakers, broken switches, and flickering lights, to the Physical Plant.
* All appliances used in TAMUS-HSC buildings must be UL (Underwriters Laboratory) or FM (Factory Mutual) labeled.
* Do not use an appliance that sparks, smokes, or becomes excessively hot, unless the appliance is specifically designed to exhibit these characteristics.
* Portable electrical heaters must be placed to avoid causing a trip hazard and must be kept away from combustible material. Never leave a heater unattended. Unplug the heater at the end of the day or when not in use.
* Keep electrical equipment away from water, unless the appliance is specifically designed for use around water, such as a wet-dry shop vacuum.
* Use GFCIs whenever possible.
* Be aware of overhead power lines when working with tall equipment.
* Follow lockout/ tag out procedures, as appropriate.
Follow these guidelines for electrical plug and cord safety:
* Do not remove the prongs of an electrical plug. If plug prongs are missing, loose, or bent, replace the entire plug.
* Do not use an adapter or extension cord to defeat a standard grounding device. (e.g., Only place three-prong plugs in three-prong outlets; do not alter them to fit in a two-prong outlet.)
* Use extension cords only when necessary and only on a temporary basis. Do not use extension cords in place of permanent wiring. Request new outlets if your work requires equipment in an area without an outlet.
* Use extension cords that are the correct size or rating for the equipment in use. The diameter of the extension cord should be the same or greater than the cord of the equipment in use.
* Do not run electrical cords above ceiling tiles or through walls.
* Keep electrical cords away from areas where they may be pinched and areas where they may pose a tripping or fire hazard (e.g., doorways, walkways, under carpet, etc.)
* Avoid plugging more than one appliance in each outlet. If multiple appliances are necessary, use an approved power strip with surge protector and circuit breaker. Do not overload the circuit breaker.
* Discard damaged cords, cords that become hot, or cords with exposed wiring.
* Never unplug an appliance by pulling on the cord; pull on the plug.
Electrical Safety: Emergency Response
The following instructions provide guidelines for handling three types of electrical emergencies:
(1) Electric Shock: when someone suffers serious electrical shock, he or she may be knocked unconscious. If the victim is still in contact with the electrical current, immediately turn off the electrical power source. If you cannot disconnect the power source, try to separate the victim from the power source with a nonconductive object, such as a wood-handled broom.
IMPORTANT: Do not touch a victim that is still in contact with a power source;
you could electrocute yourself
Have someone call for emergency medical assistance immediately. Administer
first-aid, as appropriate.
(2) Electrical Fire: if an electrical fire occurs, try to disconnect the electrical power source, if possible. If the fire is small, you are not in immediate danger, and you have been trained in fighting fires, use any type of fire extinguisher except water to extinguish the fire.
IMPORTANT: Do not use water on an electrical fire.
(3) Power Lines: Stay away from live power lines and downed power lines. Be particularly careful if a live power line is touching a body of water. The water could conduct electricity. If a power line falls on your car while you are inside, remain in the vehicle until help arrives.
Electrical Safety: Lockout/ Tagout Procedures
Lockout/tagout procedures are used to isolate hazardous energy sources from electrical, hydraulic, or pneumatic machinery. Furthermore, when service or maintenance work is required, lockout and tagout devices help ensure personal safety from possible energy releases. All employees whose work involves hazardous energy sources must be trained in lockout/tagout procedures for their specific site or contact your component’s safety officer.
Before performing service or maintenance work on machines, turn them off and disconnect them from their energy sources. To further ensure employee safety, lockout and tagout energy-isolating devices.
Applying Lockout/Tagout Devices Only authorized employees may apply lockout/tagout devices. The following steps provide a brief outline of approved application procedures:
1. Notify employees that the equipment requires service or maintenance and is scheduled for shutdown and lockout/tagout.
2. Use established procedures to identify the type, magnitude, and hazards of the equipment's energy source. Make sure you know the proper methods for controlling the energy source.
3. If the equipment is currently operating, shut it down using normal shutdown procedures.
4. Isolate the equipment from its energy source by activating the energy-isolating device(s). Either lockout or tagout the energy-isolating device(s).
5. Dissipate or restrain stored and residual energy using methods such as grounding, repositioning, blocking, bleeding, etc. (Capacitors, springs, hydraulic systems, and air/gas/water pressure system may contain stored or residual energy.)
6. Ensure that all employees are removed from the equipment. Then, test the equipment for successful isolation by attempting to operate it.
Removing Lockout/Tagout Devices
When service and maintenance are completed, authorized employees may remove lockout/tagout devices and return equipment to normal operations. The following steps provide a brief outline of approved removal procedures:
1. Inspect the work area and remove any nonessential items. Make sure the isolation equipment is intact and in good working condition.
2. Ensure that all employees are safely removed from the equipment.
3. Verify that the equipment controls are in neutral or off. Remove the lockout/tagout devices and re-energize the equipment.
4. Notify employees that the equipment is ready for operation.
Electrical Safety: High Voltage Procedures
In addition to the guidelines associated with general electrical safety and lockout/tagout procedures, there are more stringent safety requirements for high voltage procedures.
The following list provides high-voltage safety tips. For more information, please refer to Title 29 Section 1910.269 of the Code of Federal Regulations or NFPA 70 (National Electric Code).
* Ensure that only authorized employees work around high voltage equipment.
* Label entrances with a High Voltage Sign.
* Ensure that terminal voltage ratings can withstand surges caused by electrical faults or switching transients.
* Be careful around output circuits even when the input power is off. Parallel power sources and energy storage devices can still be dangerous.
* Be careful when working with power supplies that serve more than one area.
* Before working in a high voltage area, inspect the power supply and check all protective devices.
* Do not work alone near high voltage.
* Label equipment to identify power sources. Label input power sources to identify connected power supply loads.
* Attach emergency shutdown instructions and phone numbers to equipment that is remotely controlled or unattended while energized.
* Before entering a power supply or associated equipment enclosure to work on hazardous energy sources, complete the following:
o De-energize the equipment.
o Open and lockout the main input power circuit breaker.
o Check for auxiliary power circuits that could still be energized.
o Inspect automatic shorting devices for proper operation.
o Short the power supply with grounding hooks.
Electrical Safety: Minimum Clear Working Space
The following table from the National Electric Code provides minimum depth of clear working space in front of electrical equipment:
Nominal Voltage to Conditions
* 601 – 2,500 volts : i) 3 ft , ii) 4 ft, iii) 50 ft
* 2,501 – 9,000 volts : i) 4 ft , ii) 5 ft, iii) 6 ft
* 9,001 – 25,000 volts : i) 5 ft , ii) 6 ft, iii) 9 ft
* 25,001 – 75 kV : i) 6 ft , ii) 8 ft, iii) 10 ft
* Above 75 kV : i) 8 ft , ii) 10 ft, iii) 12 ft
Where conditions (i), (ii), and (iii) are as follows:
1. Exposed live parts on one side and no live or grounded parts on the other side of the working space, or exposed live parts on both sides effectively guarded by suitable wood or other insulating materials. Insulated wire or insulated bus bars operating at not over 300 volts shall not be considered live parts.
2. Exposed live parts on one side and grounded parts on the other side. Concrete, brick, or tile walls will be considered as grounded surfaces.
3. Exposed live parts on both sides of the workspace [not guarded as provided in condition (i)] with the operator between.
Thanks again Bro..... Tjetjep
present. When a person's body completes a circuit and thus connects a power source
with the ground, an electrical burn or injury is imminent. Most fatal injuries result from high-voltage exposure; however, people can sustain severe injuries from low voltage power if it has a high current flow.
Electrical safety is important in every work environment. The following sections cover circuit breaker loads, electrical grounding, electrical safety guidelines, and electrical emergency response.
Electrical Definitions
The following definitions help clarify general electrical safety:
* Amps: the standard unit for measuring electrical current.
* Watt: a unit of electrical power, equal to the power developed in a circuit by a
current of amp flowing through a potential difference of one volt.
* Voltage: electromotive force expressed in volts.
* Circuit Breaker: a device that automatically interrupts the flow of an electrical
current.
* Breaker Box: an insulated box on which interconnected circuits are mounted.
* Electrical Panel: an insulated panel on which electrical wires are mounted.
* Current Flow: the rate of flow of an electrical charge, generally expressed in amps.
* Electrical Load: the amount of power delivered by a generator or carried by a circuit. A device to which the power is delivered.
* Ground-Fault Circuit Interrupter (GFCI): a GFCI detects grounding problems
and shuts electricity off to prevent a possible accident.
* High Voltage: the term high voltage applies to electrical equipment that operates at
more than 600 Volts (for terminal to terminal operation) or more than 300 Volts (for
terminal to ground operation). Low voltage, high current AC or DC power supplies
are also considered to be high voltage.
* Hazardous Energy Sources: this term applies to stored or residual energy such as
that in capacitors, springs, elevated machine members, rotating flywheels, hydraulic
systems, and air, gas, steam, or water pressure
* Lockout: the placement of a lock on an energy-isolating device. This act prevents
workers from operating a piece of equipment until the lock is removed.
* Tagout: the placement of a tag on an energy-isolating device. A tagout device is a
prominent warning device of a lockout.
Energy-Isolating Device: a mechanical device that prevents the transmission or
release of energy.
Examples include the following:
* Manually operated circuit breakers
* Disconnect switches
* Line or block valves
Pushbuttons, selector switches, and other control circuit devices do not isolate energy. Energy-isolating devices should be lockable by means of a hasp or other type of attachment. It should not be necessary to dismantle or reassemble a device to lock it.
Authorized Employee: a person who locks out or tags out equipment for
service or maintenance. Authorized employees have been formally trained in
proper lockout/tagout procedures.
Electrical Safety : Circuit Breaker Loads
Most office and laboratory locations have 20 amp circuit breakers that serve two or
more outlets. These breakers can handle most office equipment; however, the widespread use of personal computers and associated hardware can create an electrical overload. To determine your current electrical load, follow these steps:
1. Check office/laboratory equipment for a manufacturer's rating label that indicates total watts or amps. Take special care to check appliances that use electricity to generate heat.
2. Convert the watts rating to amps: Amps = Watts ÷ 120 Volts
3. Total the amps for each circuit.
4. If the total equals more than 15 amps per 20 amp circuit, you may overloading the circuit. Move enough equipment to a different circuit to reduce the circuit load; otherwise, have the Physical Plant inspect the circuit wiring.
Electrical Safety: Electrical Grounding
Proper electrical grounding can help prevent electrical injury. Most electrical equipment is grounded with either a three-prong plug or a two-prong plug and
insulation. Because a grounding system may be defective without your knowledge,
use a GFCI to ensure electrical safety. GFCIs are required in moist or potentially damp environments.
Electrical Safety: Electrical Panels
Electrical panels or breaker boxes require special safety considerations, including the following:
* Know where your panel box is located.
* Do not tape circuit switches to keep a breaker from tripping.
* Ensure that breaker circuits are accurately labeled within panel boxes.
* Ensure that panel box doors are securely attached.
* Do not block panel boxes. There should be at least 36 inches of clear space in front of a panel box.
Report, tripped breakers and refer any electrical questions to the Physical Plant.
Electrical Safety : Guidelines
Follow these guidelines for general electrical safety:
* Be familiar with the electrical hazards associated with your workplace.
* Unplug electrical equipment before repairing or servicing it.
* If a prong breaks off inside an outlet, do not attempt to remove it yourself. Call the Physical Plant for assistance.
* Ensure that outlets are firmly mounted. Report loose outlets to the Physical Plant.
* Report all electrical problems, including tripped breakers, broken switches, and flickering lights, to the Physical Plant.
* All appliances used in TAMUS-HSC buildings must be UL (Underwriters Laboratory) or FM (Factory Mutual) labeled.
* Do not use an appliance that sparks, smokes, or becomes excessively hot, unless the appliance is specifically designed to exhibit these characteristics.
* Portable electrical heaters must be placed to avoid causing a trip hazard and must be kept away from combustible material. Never leave a heater unattended. Unplug the heater at the end of the day or when not in use.
* Keep electrical equipment away from water, unless the appliance is specifically designed for use around water, such as a wet-dry shop vacuum.
* Use GFCIs whenever possible.
* Be aware of overhead power lines when working with tall equipment.
* Follow lockout/ tag out procedures, as appropriate.
Follow these guidelines for electrical plug and cord safety:
* Do not remove the prongs of an electrical plug. If plug prongs are missing, loose, or bent, replace the entire plug.
* Do not use an adapter or extension cord to defeat a standard grounding device. (e.g., Only place three-prong plugs in three-prong outlets; do not alter them to fit in a two-prong outlet.)
* Use extension cords only when necessary and only on a temporary basis. Do not use extension cords in place of permanent wiring. Request new outlets if your work requires equipment in an area without an outlet.
* Use extension cords that are the correct size or rating for the equipment in use. The diameter of the extension cord should be the same or greater than the cord of the equipment in use.
* Do not run electrical cords above ceiling tiles or through walls.
* Keep electrical cords away from areas where they may be pinched and areas where they may pose a tripping or fire hazard (e.g., doorways, walkways, under carpet, etc.)
* Avoid plugging more than one appliance in each outlet. If multiple appliances are necessary, use an approved power strip with surge protector and circuit breaker. Do not overload the circuit breaker.
* Discard damaged cords, cords that become hot, or cords with exposed wiring.
* Never unplug an appliance by pulling on the cord; pull on the plug.
Electrical Safety: Emergency Response
The following instructions provide guidelines for handling three types of electrical emergencies:
(1) Electric Shock: when someone suffers serious electrical shock, he or she may be knocked unconscious. If the victim is still in contact with the electrical current, immediately turn off the electrical power source. If you cannot disconnect the power source, try to separate the victim from the power source with a nonconductive object, such as a wood-handled broom.
IMPORTANT: Do not touch a victim that is still in contact with a power source;
you could electrocute yourself
Have someone call for emergency medical assistance immediately. Administer
first-aid, as appropriate.
(2) Electrical Fire: if an electrical fire occurs, try to disconnect the electrical power source, if possible. If the fire is small, you are not in immediate danger, and you have been trained in fighting fires, use any type of fire extinguisher except water to extinguish the fire.
IMPORTANT: Do not use water on an electrical fire.
(3) Power Lines: Stay away from live power lines and downed power lines. Be particularly careful if a live power line is touching a body of water. The water could conduct electricity. If a power line falls on your car while you are inside, remain in the vehicle until help arrives.
Electrical Safety: Lockout/ Tagout Procedures
Lockout/tagout procedures are used to isolate hazardous energy sources from electrical, hydraulic, or pneumatic machinery. Furthermore, when service or maintenance work is required, lockout and tagout devices help ensure personal safety from possible energy releases. All employees whose work involves hazardous energy sources must be trained in lockout/tagout procedures for their specific site or contact your component’s safety officer.
Before performing service or maintenance work on machines, turn them off and disconnect them from their energy sources. To further ensure employee safety, lockout and tagout energy-isolating devices.
Applying Lockout/Tagout Devices Only authorized employees may apply lockout/tagout devices. The following steps provide a brief outline of approved application procedures:
1. Notify employees that the equipment requires service or maintenance and is scheduled for shutdown and lockout/tagout.
2. Use established procedures to identify the type, magnitude, and hazards of the equipment's energy source. Make sure you know the proper methods for controlling the energy source.
3. If the equipment is currently operating, shut it down using normal shutdown procedures.
4. Isolate the equipment from its energy source by activating the energy-isolating device(s). Either lockout or tagout the energy-isolating device(s).
5. Dissipate or restrain stored and residual energy using methods such as grounding, repositioning, blocking, bleeding, etc. (Capacitors, springs, hydraulic systems, and air/gas/water pressure system may contain stored or residual energy.)
6. Ensure that all employees are removed from the equipment. Then, test the equipment for successful isolation by attempting to operate it.
Removing Lockout/Tagout Devices
When service and maintenance are completed, authorized employees may remove lockout/tagout devices and return equipment to normal operations. The following steps provide a brief outline of approved removal procedures:
1. Inspect the work area and remove any nonessential items. Make sure the isolation equipment is intact and in good working condition.
2. Ensure that all employees are safely removed from the equipment.
3. Verify that the equipment controls are in neutral or off. Remove the lockout/tagout devices and re-energize the equipment.
4. Notify employees that the equipment is ready for operation.
Electrical Safety: High Voltage Procedures
In addition to the guidelines associated with general electrical safety and lockout/tagout procedures, there are more stringent safety requirements for high voltage procedures.
The following list provides high-voltage safety tips. For more information, please refer to Title 29 Section 1910.269 of the Code of Federal Regulations or NFPA 70 (National Electric Code).
* Ensure that only authorized employees work around high voltage equipment.
* Label entrances with a High Voltage Sign.
* Ensure that terminal voltage ratings can withstand surges caused by electrical faults or switching transients.
* Be careful around output circuits even when the input power is off. Parallel power sources and energy storage devices can still be dangerous.
* Be careful when working with power supplies that serve more than one area.
* Before working in a high voltage area, inspect the power supply and check all protective devices.
* Do not work alone near high voltage.
* Label equipment to identify power sources. Label input power sources to identify connected power supply loads.
* Attach emergency shutdown instructions and phone numbers to equipment that is remotely controlled or unattended while energized.
* Before entering a power supply or associated equipment enclosure to work on hazardous energy sources, complete the following:
o De-energize the equipment.
o Open and lockout the main input power circuit breaker.
o Check for auxiliary power circuits that could still be energized.
o Inspect automatic shorting devices for proper operation.
o Short the power supply with grounding hooks.
Electrical Safety: Minimum Clear Working Space
The following table from the National Electric Code provides minimum depth of clear working space in front of electrical equipment:
Nominal Voltage to Conditions
* 601 – 2,500 volts : i) 3 ft , ii) 4 ft, iii) 50 ft
* 2,501 – 9,000 volts : i) 4 ft , ii) 5 ft, iii) 6 ft
* 9,001 – 25,000 volts : i) 5 ft , ii) 6 ft, iii) 9 ft
* 25,001 – 75 kV : i) 6 ft , ii) 8 ft, iii) 10 ft
* Above 75 kV : i) 8 ft , ii) 10 ft, iii) 12 ft
Where conditions (i), (ii), and (iii) are as follows:
1. Exposed live parts on one side and no live or grounded parts on the other side of the working space, or exposed live parts on both sides effectively guarded by suitable wood or other insulating materials. Insulated wire or insulated bus bars operating at not over 300 volts shall not be considered live parts.
2. Exposed live parts on one side and grounded parts on the other side. Concrete, brick, or tile walls will be considered as grounded surfaces.
3. Exposed live parts on both sides of the workspace [not guarded as provided in condition (i)] with the operator between.
Thanks again Bro..... Tjetjep
Electrical Safety "Grounding"
Saya dapat ini dari sebuah Blog yang cukup bagus dan saya Post ulang...di Blog ini karena ada hubungannya dengan Blog Elctrical Instrumentation ini...
GROUNDING
A good ground connection is essential to the safe and reliable operation of any piece of electrical equipment. Electrical grounding ensures that if there is ever a short circuit on a piece of electrical equipment, current will flow through the ground system and trip a breaker or blow a fuse.
A grounded outlet has three holes for each plug. In a properly wired outlet, the rounded slot is the ground connection. A grounded outlet must be used correctly:
* Never cut off the third grounding prong on an appliance plug.
* Don’t try to install a grounded outlet in an ungrounded outlet box.
* Use “cheater” adapter plugs only on a temporary basis. Use ony if the outlet box is grounded, and make sure the small metal circle or the pigtail adapter contacts the screw in the middle of the outlet.
Ground Fault Circuit Interrupt
For an added measure of protection, outlets near water sources, like sinks and laundry appliances, as well as all garage and outdoor outlets, should have a ground fault circuit interrupter (GFCI). These are the outlets with the “test” and “reset” buttons.
A GFCI works by monitoring the flow of electricity through the outlet’s circuit. If there is any variation in the current, the GFCI will automatically cut off the flow of electricity, preventing injury. According to the Consumer Products Safety Commission, if every household used GFCIs, deaths from electrocution in and around the home could be reduced by 50 percent.
There are four types of GFCIs:
* “Whole-house” devices for circuit panels that protect against external power surges. These should be installed only by a certified electrician.
* Whole circuit devices for circuit panels, that are used in place of circuit breakers. These should be installed only by a certified electrician.
* Receptacle-based protectors that replace standard wall outlets. You can install these yourself by carefully following manufacturer’s instructions.
* “Portable” units that simply plug into a wall outlet. Any homeowner can use this type.
GFCIs should be tested every month. Plug a lamp or radio into a GFCI outlet and turn it on. Push the “test” button on the outlet; the lamp or radio should turn off immediately. If it doesn’t, the GFCI has been wired improperly or is no longer functioning.
GFCIs are inexpensive and provide the best protection against electrical hazards, and we strongly recommend using them in your home. But remember, even the best GFCI can’t offer 100% protection, so never forget other electrical safety rules
GROUNDING SYSTEM FOR ELECTRIC FENCE
The majority of electric fence problems relate to grounding concerns. This factsheet looks at the
two methods of system grounding commonly used and how to test a grounding system.
THE EFFECT OF SOIL CONDITIONS
Electric fences are designed so the animal will complete the electrical circuit upon touching the fence wire. This forms the closed circuit required for electrons to flow. For simplicity, the standard electric fence uses the earth as the “return” leg of the circuit. This is only effective if the conductivity is good, as in moist soil.
If the soil is dry, frozen or snow covered the conductivity is reduced which reduces the effectiveness of the electric fence. For areas that receive 24 inches or less annual precipitation (or where the precipitation is poorly distributed throughout the year), a “wire return” system should be used.
GROUNDING IN MOIST EARTH CONDITIONS ( Earth Return )
This is the standard grounding situation. The moisture in the earth is sufficient to allow a flow of electrical current that will ensure a shock occurs. The critical component is the soil contact of the grounding rods. They connect the earth return current flow to the controller and must have good soil contact to ensure this flow is not restricted.
This requires:
* For safety reasons, a location for the grounding system that is at least 7 feet from any other electrical or telephone grounding system and from any building foundation (especially a dairy barn) or underground water piping
* A location where the wiring cannot be easily damaged or disconnected by livestock or machinery (see below regarding burial)
* A minimum of 3 galvanized steel earthing rods, driven into moist earth; (these need not be located right at the fence controller but must be at a moist earth location)
* A separation space between the rods of 6 feet
* A continuous length of wire for connection between the rods and the controller
* A standard electrical grounding clamp (noncorrosive) for each rod/wire connection.
A grounding system that will meet the Electrical Code for grounding uses the following standard electrical components:
* Galvanized steel ground rods, 6 feet x 5/8 inch diameter,
* Brass or copper clamps, and
* #6 bare copper wire from rods to controller.
Although a smaller wire size may be adequate, a #6 wire may be directly buried which is a good method to protect the system from damage. The grounding rods can be driven 6 or 8 inches below the earth surface, say into a small dug depression. The wire can be laid into a shallow trench, clamped to the rods, then buried. The wire may be buried all the way to the fence controller.
Note that where this controller ground is near a building with an electrical service, the wire from the ground rods to the controller should be insulated to avoid ‘cross grounding’.
In addition to this main grounding of the fence controller, secondary grounding of the nonelectrified fence wire(s) may be done as explained for the “wire return” systems.
GROUNDING IN DRY EARTH CONDITIONS ( Wire Return )
In dry, frozen or snow covered conditions the earth return system is not sufficient to ensure current flow that will produce a shock.
In these conditions, one or more fence wires are used for the return circuit to the fence controller (in addition to the earth return grounding of the fence controller). This method ensures a circuit when the animal touches both an energized wire and a grounded wire (in semiwet conditions, some current may also flow via the earth return). A shock then occurs even in these poor earth return conditions (i.e. dry, frozen or snow covered).
The nonelectrified fence wire(s) are connected to the main fence controller grounding system as well as to single groundrods located approximately every ½ mile along the fence line (more frequently in very dry conditions). These ground rods are the same as the main grounding rods. To ensure the animal can easily contact a “hot” wire and a grounded wire and there by receive a shock, alternating fence wires may be electrified and grounded. However, while being more effective, it may cause maintenance problems as any debris that may contact the fence wires will more easily short out the circuit then if contacting a “hot” wire and the earth.
SALT CORE GROUND RODS
For very dry sites the main ground rods may have high resistance to current flow. This can be greatly reduced by using the following technique (which adds salt around the ground rods to increase the soil
conductivity and a clay material to hold moisture):
* Auger or dig 3 holes for the ground rods that are at least 3 inches diameter by 4 feet deep, spaced 35 feet apart
* Fill each hole with a wet slurry of 2 parts Bentonite (a clay material sometimes called “driller’s mud”) and 1 part coarse salt
* Place a 4 foot by ½ or ¾ inch diameter stainless steel tube down the center of the hole (stainless because of the corrosive nature of salt)
* Cover the area with an inch or two of sand to reduce evaporation.
The ground wire is clamped to these tubes as before.
To ensure continued low resistance, these salt core ground rods can be watered during drought conditions.
TESTING THE GROUND SYSTEM
The earth return system of grounding a fence controller relies on the soil moisture conditions for current flow and these conditions change throughout the year.
To ensure continued fence performance, a yearly grounding check should be made, preferably at the driest season the fence is being used. The following procedure should be followed:
* About 300 feet from the controller connection to the fence, use 3 or 4 steel fence posts (or similar steel material) to create a dead short from an energized wire to the earth
* This will reduce the fence line voltage to less than 1000 volts and put the grounding system under load with a high flow of electrons trying to get through the soil back to the energizer
* Using a volt meter (suitable for electric fences), measure the voltage between the ground wire to the controller and the earth at least 3 feet from any ground rod
* If the grounding system is adequate the flow will all be handled by the ground rods and the meter reading will be very low (200 volts or so)
* A higher meter reading will indicate the grounding system cannot handle the flow and more ground rods are required
* Add another ground rod and repeat the test.
(An optional method is to skip the meter and simply grasp a ground rod with one hand and touch the earth with the other hand. A poor ground is indicated with a shock, the severity of which will depend upon the condition of the grounding system. This is not recommended except for the foolhardy.)
Thanks Bro... Tjetjep
GROUNDING
A good ground connection is essential to the safe and reliable operation of any piece of electrical equipment. Electrical grounding ensures that if there is ever a short circuit on a piece of electrical equipment, current will flow through the ground system and trip a breaker or blow a fuse.
A grounded outlet has three holes for each plug. In a properly wired outlet, the rounded slot is the ground connection. A grounded outlet must be used correctly:
* Never cut off the third grounding prong on an appliance plug.
* Don’t try to install a grounded outlet in an ungrounded outlet box.
* Use “cheater” adapter plugs only on a temporary basis. Use ony if the outlet box is grounded, and make sure the small metal circle or the pigtail adapter contacts the screw in the middle of the outlet.
Ground Fault Circuit Interrupt
For an added measure of protection, outlets near water sources, like sinks and laundry appliances, as well as all garage and outdoor outlets, should have a ground fault circuit interrupter (GFCI). These are the outlets with the “test” and “reset” buttons.
A GFCI works by monitoring the flow of electricity through the outlet’s circuit. If there is any variation in the current, the GFCI will automatically cut off the flow of electricity, preventing injury. According to the Consumer Products Safety Commission, if every household used GFCIs, deaths from electrocution in and around the home could be reduced by 50 percent.
There are four types of GFCIs:
* “Whole-house” devices for circuit panels that protect against external power surges. These should be installed only by a certified electrician.
* Whole circuit devices for circuit panels, that are used in place of circuit breakers. These should be installed only by a certified electrician.
* Receptacle-based protectors that replace standard wall outlets. You can install these yourself by carefully following manufacturer’s instructions.
* “Portable” units that simply plug into a wall outlet. Any homeowner can use this type.
GFCIs should be tested every month. Plug a lamp or radio into a GFCI outlet and turn it on. Push the “test” button on the outlet; the lamp or radio should turn off immediately. If it doesn’t, the GFCI has been wired improperly or is no longer functioning.
GFCIs are inexpensive and provide the best protection against electrical hazards, and we strongly recommend using them in your home. But remember, even the best GFCI can’t offer 100% protection, so never forget other electrical safety rules
GROUNDING SYSTEM FOR ELECTRIC FENCE
The majority of electric fence problems relate to grounding concerns. This factsheet looks at the
two methods of system grounding commonly used and how to test a grounding system.
THE EFFECT OF SOIL CONDITIONS
Electric fences are designed so the animal will complete the electrical circuit upon touching the fence wire. This forms the closed circuit required for electrons to flow. For simplicity, the standard electric fence uses the earth as the “return” leg of the circuit. This is only effective if the conductivity is good, as in moist soil.
If the soil is dry, frozen or snow covered the conductivity is reduced which reduces the effectiveness of the electric fence. For areas that receive 24 inches or less annual precipitation (or where the precipitation is poorly distributed throughout the year), a “wire return” system should be used.
GROUNDING IN MOIST EARTH CONDITIONS ( Earth Return )
This is the standard grounding situation. The moisture in the earth is sufficient to allow a flow of electrical current that will ensure a shock occurs. The critical component is the soil contact of the grounding rods. They connect the earth return current flow to the controller and must have good soil contact to ensure this flow is not restricted.
This requires:
* For safety reasons, a location for the grounding system that is at least 7 feet from any other electrical or telephone grounding system and from any building foundation (especially a dairy barn) or underground water piping
* A location where the wiring cannot be easily damaged or disconnected by livestock or machinery (see below regarding burial)
* A minimum of 3 galvanized steel earthing rods, driven into moist earth; (these need not be located right at the fence controller but must be at a moist earth location)
* A separation space between the rods of 6 feet
* A continuous length of wire for connection between the rods and the controller
* A standard electrical grounding clamp (noncorrosive) for each rod/wire connection.
A grounding system that will meet the Electrical Code for grounding uses the following standard electrical components:
* Galvanized steel ground rods, 6 feet x 5/8 inch diameter,
* Brass or copper clamps, and
* #6 bare copper wire from rods to controller.
Although a smaller wire size may be adequate, a #6 wire may be directly buried which is a good method to protect the system from damage. The grounding rods can be driven 6 or 8 inches below the earth surface, say into a small dug depression. The wire can be laid into a shallow trench, clamped to the rods, then buried. The wire may be buried all the way to the fence controller.
Note that where this controller ground is near a building with an electrical service, the wire from the ground rods to the controller should be insulated to avoid ‘cross grounding’.
In addition to this main grounding of the fence controller, secondary grounding of the nonelectrified fence wire(s) may be done as explained for the “wire return” systems.
GROUNDING IN DRY EARTH CONDITIONS ( Wire Return )
In dry, frozen or snow covered conditions the earth return system is not sufficient to ensure current flow that will produce a shock.
In these conditions, one or more fence wires are used for the return circuit to the fence controller (in addition to the earth return grounding of the fence controller). This method ensures a circuit when the animal touches both an energized wire and a grounded wire (in semiwet conditions, some current may also flow via the earth return). A shock then occurs even in these poor earth return conditions (i.e. dry, frozen or snow covered).
The nonelectrified fence wire(s) are connected to the main fence controller grounding system as well as to single groundrods located approximately every ½ mile along the fence line (more frequently in very dry conditions). These ground rods are the same as the main grounding rods. To ensure the animal can easily contact a “hot” wire and a grounded wire and there by receive a shock, alternating fence wires may be electrified and grounded. However, while being more effective, it may cause maintenance problems as any debris that may contact the fence wires will more easily short out the circuit then if contacting a “hot” wire and the earth.
SALT CORE GROUND RODS
For very dry sites the main ground rods may have high resistance to current flow. This can be greatly reduced by using the following technique (which adds salt around the ground rods to increase the soil
conductivity and a clay material to hold moisture):
* Auger or dig 3 holes for the ground rods that are at least 3 inches diameter by 4 feet deep, spaced 35 feet apart
* Fill each hole with a wet slurry of 2 parts Bentonite (a clay material sometimes called “driller’s mud”) and 1 part coarse salt
* Place a 4 foot by ½ or ¾ inch diameter stainless steel tube down the center of the hole (stainless because of the corrosive nature of salt)
* Cover the area with an inch or two of sand to reduce evaporation.
The ground wire is clamped to these tubes as before.
To ensure continued low resistance, these salt core ground rods can be watered during drought conditions.
TESTING THE GROUND SYSTEM
The earth return system of grounding a fence controller relies on the soil moisture conditions for current flow and these conditions change throughout the year.
To ensure continued fence performance, a yearly grounding check should be made, preferably at the driest season the fence is being used. The following procedure should be followed:
* About 300 feet from the controller connection to the fence, use 3 or 4 steel fence posts (or similar steel material) to create a dead short from an energized wire to the earth
* This will reduce the fence line voltage to less than 1000 volts and put the grounding system under load with a high flow of electrons trying to get through the soil back to the energizer
* Using a volt meter (suitable for electric fences), measure the voltage between the ground wire to the controller and the earth at least 3 feet from any ground rod
* If the grounding system is adequate the flow will all be handled by the ground rods and the meter reading will be very low (200 volts or so)
* A higher meter reading will indicate the grounding system cannot handle the flow and more ground rods are required
* Add another ground rod and repeat the test.
(An optional method is to skip the meter and simply grasp a ground rod with one hand and touch the earth with the other hand. A poor ground is indicated with a shock, the severity of which will depend upon the condition of the grounding system. This is not recommended except for the foolhardy.)
Thanks Bro... Tjetjep
Minggu, 27 Juli 2008
Aku dan Keluargaku II
...sambungan...
Tak terasa hampir 9 tahun sudah kami tinggal di Mataram....dari Januari 2000 hingga sekarang.
9 tahun juga aku Pulang pergi Lombok - Sumbawa untuk menunaikan tugas dan kewajibanku bekerja di sebuah Tambang Emas dan Tembaga yang site-nya berada di Sumbawa Barat, tepatnya di Batu Hijau Project.
Aku...seorang pekerja yang dengan Background pendidikan dan pengalaman dalam penanganan Electrical, Control dan Instrumentation...jadi selama hampir 13 tahun bekerja di 2 perusahaan PMA (BHP Steel Indonesia dan Newmont Nusa Tenggara) selalu berada di department yang memang khusus untuk menangani Tekhnik Electrical, Control dan Instrumentation...(maaf jika dari anda ada yang membutuhkan seseorang yang bisa menangani Tekhnik Electrical, Control dan Instrumentation di tempat anda bekerja silahkan lihat CV saya atau contact ke email ..."promosi"..! )
Tak terasa hampir 9 tahun sudah kami tinggal di Mataram....dari Januari 2000 hingga sekarang.
9 tahun juga aku Pulang pergi Lombok - Sumbawa untuk menunaikan tugas dan kewajibanku bekerja di sebuah Tambang Emas dan Tembaga yang site-nya berada di Sumbawa Barat, tepatnya di Batu Hijau Project.
Aku...seorang pekerja yang dengan Background pendidikan dan pengalaman dalam penanganan Electrical, Control dan Instrumentation...jadi selama hampir 13 tahun bekerja di 2 perusahaan PMA (BHP Steel Indonesia dan Newmont Nusa Tenggara) selalu berada di department yang memang khusus untuk menangani Tekhnik Electrical, Control dan Instrumentation...(maaf jika dari anda ada yang membutuhkan seseorang yang bisa menangani Tekhnik Electrical, Control dan Instrumentation di tempat anda bekerja silahkan lihat CV saya atau contact ke email ..."promosi"..! )
Sabtu, 26 Juli 2008
Electron
An electron is a negatively charged subatomic particle. It can be either free (not attached to any atom), or bound to the nucleus of an atom. Electrons in atoms exist in spherical shells of various radii, representing energy levels. The larger the spherical shell, the higher the energy contained in the electron.
In electrical conductors, current flow results from the movement of electrons from atom to atom individually, and from negative to positive electric poles in general. In semiconductor materials, current also occurs as a movement of electrons. But in some cases, it is more illustrative to envision the current as a movement of electron deficiencies from atom to atom. An electron-deficient atom in a semiconductor is called a hole. Holes "move" from positive to negative electric poles in general.
The charge on a single electron is considered as the unit electrical charge. It is assigned negative polarity. The charge on an electron is equal, but opposite, to the positive charge on a proton or hole. Electrical charge quantity is not usually measured in terms of the charge on a single electron, because this is an extremely small charge. Instead, the standard unit of electrical charge quantity is the coulomb, symbolized by C, representing about 6.24 x 1018 electrons. The electron charge, symbolized by e, is about 1.60 x 10-19 C. The mass of an electron at rest, symbolized me, is approximately 9.11 x 10-31 kilogram (kg). Electrons moving at an appreciable fraction of the speed of light, for example in a particle accelerator, have greater mass because of relativistic effectsAPLIKASI MIKRO KONTROLER AT89C51 UNTUK MENGENDALIKAN KECEPATAN MOTOR SINKRON TIGA FASE DI FLOPPY DISK DRIVE MENGGUNAKAN BAHASA PEMROGRAMAN "C"
PENDAHULUAN
Floppy disk drive (FDD) merupakan salah satu bagian dari komputer yang menggunakan motor sebagai salah satu komponen utamanya. Motor yang digunakan di sini adalah motor sinkron 3 fase yang termasuk di dalam keluarga motor AC. Motor sinkron ini digunakan untuk memutar piringan yang berisi data dengan kecepatan tertentu. Dalam aplikasinya motor sinkron FDD digerakan oleh suatu IC driver yang berkerja pada rating tegangan komputer yaitu 12 V dan motor AC yang bekerja pada rating tegangan yang kecil merupakan suatu hal yang jarang ditemui Karena termasuk jenis motor AC maka motor sinkron memerlukan catu daya AC dengan besar tegangan dan frekuensi tertentu. Pengendalian kecepatan putaran motor induksi dapat dilakukan dengan beberapa cara, salah satunya dengan mengendalikan tegangan dan frekuensi pada sinyal masukan AC.
Sekarang pengendalian dan pembangkitan sinyal AC sinusoidal akan dilakukan dengan menggunakan mikrokontroler atau DSP (Digital Signal Processing). Mikrokontroler yang nantinya akan menggantikan fungsi kerja dari IC penggerak motor FDD akan memberikan keuntungan dalam hal fleksibilitas dan reabilitas.
Sampai sekarang pemrograman mikrokontroler banyak dilakukan dengan menggunakan bahasa assembler. Namun seiring dengan perkembangan teknologi, pemrograman mikrokontroler dengan bahasa pemrograman tingkat yang lebih tinggi sudah bisa dilakukan, tergantung dari keberadaan program yang bisa menerjemahkan bahasa tersebut menjadi bahasa mesin yang dapat dimengerti oleh mikrokontroler. Program-program kompiler yang lebih maju telah mulai diciptakan sehingga sekarang ini mikrokontroler bisa diprogram dengan menggunakan bahasa-bahasa pemrograman yang lebih umum seperti Pascal atau C.
C merupakan salah satu bahasa pemrograman tingkat tinggi yang sudah umum sekali dipakai. Banyak pembuat program menyukai penggunaan bahasa C karena fleksibilitas, kesederhanaan, kebebasan, dan juga keteraturan struktur yang dimiliki oleh bahasa ini. Pihak Microsoft sendiri menggunakan C untuk membuat program sumber sistem operasi Microsoft Windows. Hal ini menunjukkan bahwa bahasa C memiliki kekuatan dan kelebihan tersendiri dibandingkan dengan bahasa pemrograman lainnya. Kelebihan ini jugalah yang membuat pemrograman mikrokontroler dengan bahasa C mulai dilakukan.
Dasar teori
Teori-teori dasar yang digunakan dalam tugas akhir ini adalah teori-teori mengenai motor sinkron, DAC, untai penguat-penjumlah, penguat push-pull, mikrokontroler, serta perangkat lunak yang digunakan untuk membuat rancangan dan melakukan simulasi.
Metodologi Penelitian
Penelitian tugas akhir ini dilakukan dengan menggunakan metode-metode sebagai berikut:
1. Studi pustaka; mendapatkan semua teori-teori dasar yang dibutuhkan dalam perancangan perangkat lunak dan perangkat keras untuk mengimplementasikan ide penelitian.
2. Perancangan perangkat lunak; menggunakan teori-teori dasar perangkat lunak yang digunakan dan menggunakan logika berpikir untuk menghasilkan program kendali kecepatan motor.
3. Perancangan perangkat keras; menggunakan teori-teori dasar elektronika untuk menghasilkan perangkat keras yang mampu menjalankan fungsi yang diinginkan untuk mencapai tujuan penelitian.
4. Pengambilan data; pengimplementasian integrasi hasil rancangan perangkat lunak dan keras lalu melakukan pengamatan dan pengambilan data untuk menghasilkan sebuah laporan penelitian yang bertujuan untuk memberikan pemahaman atas ide penelitian tersebut.
Hasil Implementasi dan Pembahasan
Data hasil pengamatan dari implementasi rancangan yang telah dibuat menunjukkan hal-hal sebagai berikut:
1. Motor sinkron 3 fase di FDD mampu diputar hingga kecepatan 1138 rpm dengan VPP sinyal penggerak sinus 30 V, walaupun dalam aplikasi nyata biasanya motor FDD diputar pada kecepatan 300-360 rpm
2. Sesuai dengan daerah kerja motor, sistem kendali kecepatan motor FDD dengan mikrokontroler AT89C51 mampu menghasilkan frekuensi sinus 3 fase dari 1-95,2 Hz.
3. Didapatkan suatu data statistik yang menunjukkan dengan T = periode sinyal sinus (µs);
n = jumlah cuplikan untuk 1 siklus sinyal sinus;
d = jumlah loop program delay yang diproses mikrokontroler.
Waktu yang dibutuhkan mikrokontroler untuk melakukan proses pengambilan 1 data adalah sekitar 127,54µs (nilai pendekatan) dan waktu yang dibutuhkan mikrokontroler untuk melakukan 1 loop subrutin delay adalah sekitar 18,78µs (nilai pendekatan).
4. Didapat pula dari data satistik hasil pengamatan bahwa:
n = 12f + 1,5
dengan n = kecepatan putaran motor (rpm);
f = frekuensi sinyal sinus penggerak (Hz).
Kesimpulan
Dari hasil simulasi, pengamatan dan pengujian pada implementasi rancangan yang dibuat dapat diperoleh kesimpulan sebagai berikut :
3. Kecepatan motor sinkron 3 fase di floppy disk drive (FDD) dapat dikendalikan dengan baik menggunakan mikrokontroler AT89C51.
4. Bahasa C untuk memrogram mikrokontroler AT89C51 memiliki tingkat efisiensi dan keandalan yang baik. Dapat dilihat dari lampiran B bahwa program kendali motor FDD bila dilakukan dengan bahasa assembler akan memiliki baris program yang jauh lebih panjang daripada bahasa C.
5. Frekuensi sinus 3 fase penggerak dengan kecepatan motor yang dihasilkan memiliki perbandingan lurus satu sama lain, sedangkan frekuensi sinus penggerak berbanding lurus dengan jumlah loop subprogram tunda dalam program kendali motor FDD.
6. Berdasarkan hasil percobaan, studi pustaka, dan analisis hasil pengamatan maka didapatkan suatu perumusan motor sinkron 3 fase di FDD sebagai berikut:
dengan nm = kecepatan putar rotor (rpm)
fe = frekuensi sinus 3 fase penggerak di stator (Hz)
pe = jumlah kutub di stator
pm = jumlah kutub di rotor
k = konstanta rugi-rugi
"Tjetjep"
Floppy disk drive (FDD) merupakan salah satu bagian dari komputer yang menggunakan motor sebagai salah satu komponen utamanya. Motor yang digunakan di sini adalah motor sinkron 3 fase yang termasuk di dalam keluarga motor AC. Motor sinkron ini digunakan untuk memutar piringan yang berisi data dengan kecepatan tertentu. Dalam aplikasinya motor sinkron FDD digerakan oleh suatu IC driver yang berkerja pada rating tegangan komputer yaitu 12 V dan motor AC yang bekerja pada rating tegangan yang kecil merupakan suatu hal yang jarang ditemui Karena termasuk jenis motor AC maka motor sinkron memerlukan catu daya AC dengan besar tegangan dan frekuensi tertentu. Pengendalian kecepatan putaran motor induksi dapat dilakukan dengan beberapa cara, salah satunya dengan mengendalikan tegangan dan frekuensi pada sinyal masukan AC.
Sekarang pengendalian dan pembangkitan sinyal AC sinusoidal akan dilakukan dengan menggunakan mikrokontroler atau DSP (Digital Signal Processing). Mikrokontroler yang nantinya akan menggantikan fungsi kerja dari IC penggerak motor FDD akan memberikan keuntungan dalam hal fleksibilitas dan reabilitas.
Sampai sekarang pemrograman mikrokontroler banyak dilakukan dengan menggunakan bahasa assembler. Namun seiring dengan perkembangan teknologi, pemrograman mikrokontroler dengan bahasa pemrograman tingkat yang lebih tinggi sudah bisa dilakukan, tergantung dari keberadaan program yang bisa menerjemahkan bahasa tersebut menjadi bahasa mesin yang dapat dimengerti oleh mikrokontroler. Program-program kompiler yang lebih maju telah mulai diciptakan sehingga sekarang ini mikrokontroler bisa diprogram dengan menggunakan bahasa-bahasa pemrograman yang lebih umum seperti Pascal atau C.
C merupakan salah satu bahasa pemrograman tingkat tinggi yang sudah umum sekali dipakai. Banyak pembuat program menyukai penggunaan bahasa C karena fleksibilitas, kesederhanaan, kebebasan, dan juga keteraturan struktur yang dimiliki oleh bahasa ini. Pihak Microsoft sendiri menggunakan C untuk membuat program sumber sistem operasi Microsoft Windows. Hal ini menunjukkan bahwa bahasa C memiliki kekuatan dan kelebihan tersendiri dibandingkan dengan bahasa pemrograman lainnya. Kelebihan ini jugalah yang membuat pemrograman mikrokontroler dengan bahasa C mulai dilakukan.
Dasar teori
Teori-teori dasar yang digunakan dalam tugas akhir ini adalah teori-teori mengenai motor sinkron, DAC, untai penguat-penjumlah, penguat push-pull, mikrokontroler, serta perangkat lunak yang digunakan untuk membuat rancangan dan melakukan simulasi.
Metodologi Penelitian
Penelitian tugas akhir ini dilakukan dengan menggunakan metode-metode sebagai berikut:
1. Studi pustaka; mendapatkan semua teori-teori dasar yang dibutuhkan dalam perancangan perangkat lunak dan perangkat keras untuk mengimplementasikan ide penelitian.
2. Perancangan perangkat lunak; menggunakan teori-teori dasar perangkat lunak yang digunakan dan menggunakan logika berpikir untuk menghasilkan program kendali kecepatan motor.
3. Perancangan perangkat keras; menggunakan teori-teori dasar elektronika untuk menghasilkan perangkat keras yang mampu menjalankan fungsi yang diinginkan untuk mencapai tujuan penelitian.
4. Pengambilan data; pengimplementasian integrasi hasil rancangan perangkat lunak dan keras lalu melakukan pengamatan dan pengambilan data untuk menghasilkan sebuah laporan penelitian yang bertujuan untuk memberikan pemahaman atas ide penelitian tersebut.
Hasil Implementasi dan Pembahasan
Data hasil pengamatan dari implementasi rancangan yang telah dibuat menunjukkan hal-hal sebagai berikut:
1. Motor sinkron 3 fase di FDD mampu diputar hingga kecepatan 1138 rpm dengan VPP sinyal penggerak sinus 30 V, walaupun dalam aplikasi nyata biasanya motor FDD diputar pada kecepatan 300-360 rpm
2. Sesuai dengan daerah kerja motor, sistem kendali kecepatan motor FDD dengan mikrokontroler AT89C51 mampu menghasilkan frekuensi sinus 3 fase dari 1-95,2 Hz.
3. Didapatkan suatu data statistik yang menunjukkan dengan T = periode sinyal sinus (µs);
n = jumlah cuplikan untuk 1 siklus sinyal sinus;
d = jumlah loop program delay yang diproses mikrokontroler.
Waktu yang dibutuhkan mikrokontroler untuk melakukan proses pengambilan 1 data adalah sekitar 127,54µs (nilai pendekatan) dan waktu yang dibutuhkan mikrokontroler untuk melakukan 1 loop subrutin delay adalah sekitar 18,78µs (nilai pendekatan).
4. Didapat pula dari data satistik hasil pengamatan bahwa:
n = 12f + 1,5
dengan n = kecepatan putaran motor (rpm);
f = frekuensi sinyal sinus penggerak (Hz).
Kesimpulan
Dari hasil simulasi, pengamatan dan pengujian pada implementasi rancangan yang dibuat dapat diperoleh kesimpulan sebagai berikut :
3. Kecepatan motor sinkron 3 fase di floppy disk drive (FDD) dapat dikendalikan dengan baik menggunakan mikrokontroler AT89C51.
4. Bahasa C untuk memrogram mikrokontroler AT89C51 memiliki tingkat efisiensi dan keandalan yang baik. Dapat dilihat dari lampiran B bahwa program kendali motor FDD bila dilakukan dengan bahasa assembler akan memiliki baris program yang jauh lebih panjang daripada bahasa C.
5. Frekuensi sinus 3 fase penggerak dengan kecepatan motor yang dihasilkan memiliki perbandingan lurus satu sama lain, sedangkan frekuensi sinus penggerak berbanding lurus dengan jumlah loop subprogram tunda dalam program kendali motor FDD.
6. Berdasarkan hasil percobaan, studi pustaka, dan analisis hasil pengamatan maka didapatkan suatu perumusan motor sinkron 3 fase di FDD sebagai berikut:
dengan nm = kecepatan putar rotor (rpm)
fe = frekuensi sinus 3 fase penggerak di stator (Hz)
pe = jumlah kutub di stator
pm = jumlah kutub di rotor
k = konstanta rugi-rugi
Thesis Pak DONNY LESMANA
Disadur dari : www.te.ugm.ac.id/~bsutopo/DONI.doc
http://sdcc.sourceforge.net
Disadur dari : www.te.ugm.ac.id/~bsutopo/DONI.doc
http://sdcc.sourceforge.net
"Tjetjep"
Jumat, 25 Juli 2008
Pengantar Pengendalian Proses "Bab I"
PENGANTAR PENGENDALIAN PROSES
1.1. PENDAHULUAN
Ketika kita melakukan pengamatan pada proses kimia di pabrik atau
laboratorium, maka terdapat banyak aliran dari vessel ke vessel, gelembung cairan dan material viscous serta semua alat berubah secara terus menerus. Dengan perubahan sedikit saja maka bisa terdapat respon yang berakibat fatal. Kesimpulan dari wacana sementara ini adalah bahwa dunia adalah sebuah dinamika dan ini merupakan alasan yang tepat untuk adanya sebuah proses kontrol. Dalam memahami perilaku sistem maka seorang engineer process design dapat memahami prilaku dinamiknya.
Teknik pengontrolan adalah ilmu teknik yang digunakan pada banyak aplikasi misalnya kimia, listrik dan teknik mesin serta diterapkan pada berbagai sistem fisik mulai dari sirkuit elektrik sampai pada perancangan robot. Dalam bidang ilmu teknik kimia proses kontrol diterapkan pada disain reaktor, Heat exchanger, dan peralatan transfer massa lainnya.
Proses kontrol adalah topik esensial bagi seorang chemical engineers misalnya pada perancangan pabrik yang harus mempertimbangkan prilaku dinamik pada semua peralatan karena pabrik tidak beroperasi secara steady state.
Engineers yang bertanggung jawab pada beroperasinya pabrik harus
memastika bahwa respon yang terjadi akibat adanya gangguan harus bsa diatasi agar tetap aman dan menguntungkan.
Kesimpulannya tugas seorang engineers untuk mendisain, membangun dan
mengoperasikan sistem fisik adalah sebuah aktivitas untuk menjaga sistem pada kondisi yang diinginkan.
Teknik proses kontrol meliputi analisis matematika dan praktek teknik,
sebelum kita memahami tujuan dari prinsip proses kontrol dan perhitungannya maka kita harus mengetahui tujuan dari proses kontrol dan hubungannya dengan teknik kimia. Bab ini akan membahas mengenai pertanyaan- pertanyaan sebagai berikut :
Ø Apa saja yang dilakukan proses kontrol?
Ø Mengapa diperlukan proses kontrol?
Ø Mengapa dimngkinkan adanya proses kontrol?
Ø Bagaimana proses kontrol dilakukan?
Ø Dimana sistem kontrol diterapkan?
Ø Apa saja yang dilakukan control engineer?
Ø Bagaimana proses kontrol didokumentasikan?
Ø Apa saja contoh dari sistem kontrol yang strategis?
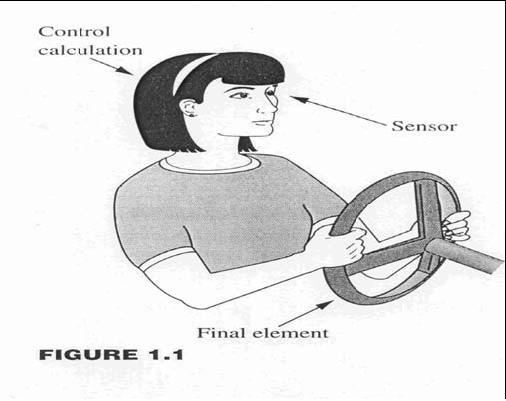
1.2. Apa saja yang dilakukan oleh proses kontrol ?
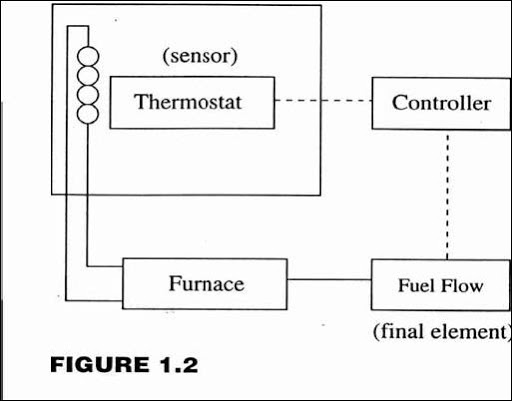
Pertama tama kita akan mendiskusikan mengenai 2 contoh dari sistem kontrol yang terdapat dalam kehidupan kita sehari-hari kemudian kita akan mendiskusikan mengenai sistem yang lebih umum dalam defenisi sistem kontrol dan feedback kontrol.
Contoh pertama adalah orang yang mengendarai mobil seperti yang ditunjukan oleh Gambar 1.1. Supir harus memiliki tujuan atau objektif. Pertama tama supir harus menentukan lokasi dari mobil di jalan dengan menggunkan mata untuk melihat posisi mobil di jalan kemudian supir juga harus memperhitungkan keaadan agar menjaga mobil tetap pada posisi yang diinginkan di jalan dan akhirnya supir haruslah mengubah posisi mobil dengan menggunakan stir. Dengan mengunakan ketiga cara ini maka supir bisa menjaga mobil tetap berada pada posisi ynang diinginkan.
Contoh kedua adalah sistem pemanas sederhana seperti yang ditunjukan
gambar 1.2. Rumah yang berada pada daerah beriklim dingin bisa menaikan suhu dengan menggunakan pemanas. Temperatur dalam ruangan diukur oleh termostat yang kemudian membandingkannya dengan temperatur ruang pada range yang diinginkan, katakanlah 18 sampai 22oC. Jika temperature dibawah 18oC, furnace dan pompa akan menyala, dan jika temperature di atas 22oC, furnace dan pompa akan berhenti bekerja. Jika temperature diantara 18 sampai 22oC,kondisi furnace dan pompa tidak akan berubah. Secara umum prilaku dari kondisi temperature dalam rumah diberikan dalam figure 1.3, yang menunjukkan bagaimana temperature
bergeser secara perlahan dari batas atas dan bawah. Dapat dilihat juga bahwa ada suatu saat prilaku temperature melewati batas-batas tersebut, karena furnace dan heat exchanger tidak memberikan respons secepatnya. Pendekatan ini dinamakan “on/off”control dan dapat digunakan sewaktu control yang akurat pada nilai yang diinginkan tidak diperlukan. Kita akan membahas metode pengontrolan yang lebih baik di bagian berikutnya, dimana dapat mempertahankan variable yang penting cukup dekat pada nilai yang diinginkan.
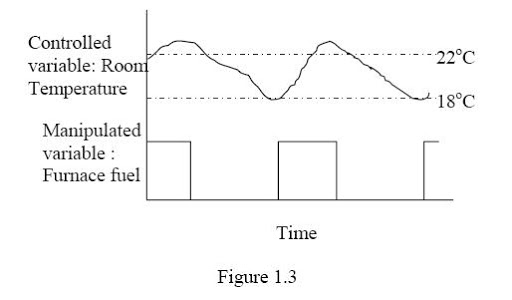
Setelah tadi kita membahas secara sekilas mengenai dua sistem control,
kemudian kita akan mengidentifikasikan beberapa fitur umum. Yang pertama adalah tiap sistem menggunakan nilai yang spesifik (atau range) sebagai nilai yang diinginkan sebagai variable yang dikontrol. Sewaktu kita membahas kalkulasi control dalam Bagian III, kita akan menggunakan istilah set point untuk nilai yang diinginkan. Yang kedua, Kondisi dari sistem diukur; yakni semua sistem control menggunakan sensor untuk mengukur variable fisis yang akan dijaga dekat dengan nilai yang diinginkan. Yang ketiga, tiap sistem mempunyai kalkulasi control, atau
algoritma, dimana menggunakan hasil pengukuran dan nilai yang diinginkan untuk menentukan koreksi pada proses operasi. Kalkulasi control untuk pemanas ruangan adalah contoh yang sangat sederhana (on/off), sedangkan control yang digunakan pada contoh “si pengemudi” akan sangat kompleks. Akhirnya, hasil kalkulasi akan diimplentasikan dengan mengeset salah satu alat pada sistem, dimana istilahnya adalah final control element, seperti setir mobil atau tombol saklar furnace dan pompa. Kunci fitur tersebut ditunjukkan secara skematik pada figure 1.4, dimana
dapat digunakan untuk merepresentasikan banyak sistem control.
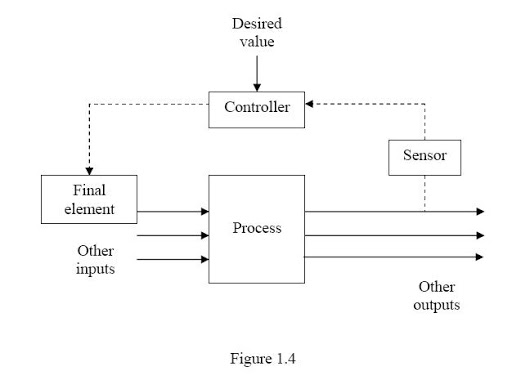
Setelah tadi kita membahas beberapa sistem control umum dan mengidentifikasikan kunci fitur, sekarang kita akan mendefinisikan istilah control. Kamus meberikan definisi untuk kata control sebagai “untuk mempengaruhi secara langsung”. Kita akan menggunakan definisi yang mirip dalam penerapan keperluan kita. Definisi berikut ini cocok untuk dua contoh fisis dan representasi skematik pada figure 1.4.
Control(verb): untuk mempertahankan kondisi yang diinginkan dalam sistem fisis dengan mengatur variable tertentu dalam sistem.
Contoh control mempunyai fitur tambahan yang amat penting. Itu adalah
feedback, yang didefinisikan sebagai berikut:
Feedback control menggunakan hasil keluaran output dari sistem untuk
mempengaruhi input dari sistem yang sama.
Sebagai contoh, temperatur ruangan yang digunakan, melewati keputusan
on/off thermostat, untuk mempengaruhi aliran air panas menuju heat exchanger. Sewaktu feedback digunakan untuk mengurangi perbedaan antara nilai aktual dan nilai yang diinginkan, ini dinamakan dengan “negative feedback”. Kecuali dinyatakan lain, maka kita selalu mendiskusikan negative feedback dan tidak akan menggunakan kata ‘negatif’. Dalam ilmu sosial dan vernacular umum, frasa “negative feedback” mengindikasikan perubahan yang tidak diinginkan, karena sebagian besar orang tidak menikmati menerima sinyal yang menyatakan mereka untuk mengoreksi kesalahan. Sebagian besar orang lebih suka menerima “positive feedback”, sinyal yang menyatakan mereka untuk melanjutkan kecenderungan untuk mencapai kondisi yang diinginkan. Perbedaan dalam terminologi ini sangat disayangkan; kita akan menggunakan terminologi pada kontrol otomatis, dimana “negatif” mengindikasikan perubahan yang bertujuan untuk mencapai nilai yang diinginkan diseluruh isi buku ini, tanpa kecuali.
Kegunaan penting dari feedback pada sistem kontrol dapat dilihat dengan
menganggap suatu alternatif tanpa feedback. Sebagai contoh, pendekatan alternatif dari pengaturan suhu ruangan yang diinginkan akan dilakukan dengan mengeset aliran air panas berdasarkan pengukuran temperatur luar ruangan dan model untuk kehilangan panas dari dalam ruangan. (tipe alternatif ini dinamakan feedforward, akan dibahas belakangan di buku ini, dimana penggunaannya bersamaan dengan feedback akan dibahas). Strategi tanpa feedback untuk mempertahankan suhu ruangan takkan
berhasil bila model tersebut mempunyai error—seperti yang biasanya terjadi. Beberapa penyebab dari error bisa disebabkan oleh kecepatan angin dan alian udara dari jendela yang terbuka. Di lain pihak, feedback dapat selalu memanipulasi final element untuk mencapai nilai yang diinginkan. Oleh karena itu, feedback menyediakan fitur yang kuat agar sistem kontrol dapat mencapai nilai terukur dekat dengan nilai yang diinginkan tanpa memerlukan model plant secara tepat.
Sebelum kita menyelesaikan bagian ini, istilah input dan output harus
diklarifikasikan. Sewaktu digunakan dalam pembahasan sistem kontrol, input dan output tidak ditujukan untuk material yang bergerak masuk dan keluar sistem. Disini istilah input ditujukan untuk variabel yang menyebabkan output. Dalam contoh ‘mengemudi’ input adalah posisi setir dan output adalah posisi mobil. Pada contoh pemanas ruangan, input adalah bahan bakar untuk furnace dan output adalah temperatur ruangan. Sangat penting untuk diketahui bahwa input menyebabkan output dan hubungan ini tidak dapat dibalik. Hubungan sebab-akibat yang timbul pada proses fisis memaksa kita untuk memilih input sebagai variabel manipulasi dan output sebagai variabel terukur. Banyak contoh dengan seleksi dari variabel kontrol dan variabel manipulasi akan ditampilkan dalam chapter berikut.
Oleh karena itu, jawaban untuk pertanyaan pertama mengenai fungsi kontrol adalah,” sistem kontrol feedback mempertahankan variabel spesifik dekat dengan nilai yang diinginkan dengan mengaplikasikan empat fitur dasar ditunjukkan dalam figur1.4.” Memahami dan mendesain sistem kontrol feedback merupakan tujuan utama dari buku ini.
1.3 Kenapa kontrol diperlukan?
Sebuah pertanyaan alami kedua terlibat kebutuhan akan kontrol. Ada dua
alasan utama untuk kontrol, dimana akan didiskusikan dengan respek untuk tangki berpengaduk yang sederhana dengan penukar panas yang digambarkan pada gambar1.5. Fluida proses mengalir ke dalam tangki dari sebuah pipa dan mengalir keluar dari tangki oleh aliran berlebih. Oleh karena itu, volume tangki konstan. Fluida pemanas mengalir dapat diatur dengan mengubah bukaan keran pada media aliran pemanas. Suhu dalam tangki dapat dikontrol.
Alasan pertama kontrol ialah untuk mempertahankan suhu pada nilai yang
diinginkan ketika gangguan muncul. Beberapa ganggguan khas untuk proses ini terjadi pada variabel berikut: laju alir dan suhu fluida proses masukan, suhu fluida pemanas dan tekanan aliran pemanas upstream dari keran. Sebagai latihan, anda sebaiknya menentukan bagaimana keran harus diatur (dibuka dan ditutup) pada respon utnuk meningkatkan pada tiap-tiap varibel gangguan tersebut.
Alasan kedua kontrol ialah untuk merespon perubahan pada nilai yang
diinginkan. Sebagai contoh, jika suhu yang diinginkan pada tangki berpengaduk dengan penukar panas ditingkatkan, persentase keran pemanas harus ditingkatkan. Nilai yang diinginkan berdasar pada analisis operasi pabrik dan sasaran. Analisis ini akan didiskusikan dalam bab 2, dimana topik utama diatur dalam tujuh kategori:
1. keselamatan
2. perlindungan lingkungan
3. perlindungan peralatan
4. operasi pabrik yang mulus dan laju produksi
5. kualitas produk
6. optimalisasi laba
7. pengawasan dan diagnosis
Topik ini ditranslasikan pada nilai variabel – suhu, tekanan, aliran, dan selanjutnya – dimana dapat dikontrol.
1.4 kenapa kontrol memungkinkan?
Desain yang tepat dari peralatan pabrik sangat penting untuk kontrol yang
memungkinkan dan untuk kontrol memberikan kinerja dinamik yang baik. Oleh karena itu, kontrol dan operasi dinamis merupakan faktor yang sangat penting pada desain pabrik. Berdasar pada fitur kunci dari kontrol umpan balik pada gambar1.4, desain pabrik harus termasuk sensor yang cukup dari variabel keluaran pabrik dan elemen kontrol final. Sensor harus merespon secara cepat sehingga aksi kontrol dapat diambil dalam waktu nyata. Sensor menggunakan variasi prinsip fisik yang ada untuk variabel proses dasar (aliran, suhu, tekanan, dan level), komposisi (seperti fraksi mol)
dan sifat fisik (densitas, viskositas, kalor pembakaran). Banyak sensor disertakan pada peralatan proses, dengan sebuah pelapis melindungi mereka dari efek korosi dari aliran. Yang lain membutuhkan sampel diambil secara periodik dari proses; sebagai catatan sampling ini dapat secara otomatis sehingga hasil sensor baru ada untuk interval frekuensi. Elemen kontrol final dari proses kimia biasanya berupa keran mempengaruhi aliran fluida, tetapi mereka dapat merupakan variabel manipulasi lainnya, seperti tenaga untuk motor elektrik atau kecepatan pada sabuk pemutar.
Pemikiran penting lainnya ialah kapasitas dari peralatan proses. Peralatan
harus mempunyai kapasitas yang cukup besar untuk merespon semua gangguan yang diharapkan dan perubahan pada nilai yang diinginkan. Untuk tangki berpengaduk dengan penukar panas, tugas maksimum, yang dipengaruhi oleh suhu, area dan laju alir media pemanas, harus cukup besar untuk mempertahankan suhu tangki untuk mengantisipasi semua gangguan. Tugas yang paling besar berhubungan dengan suhu keluaran maksimum, aliran fluida maksimum, suhu fluida masukan terendah, dan
kehilangan kalor maksimum ke lingkungan. Setiap proses harus dianalisa untuk meyakinkan kapasitas yang tepat. Diskusi lebih lanjut dari topik ini muncul pada dua bab selanjutnya.
Alhasil, sebagai jawaban kenapa kontrol memungkinkan ialah kita mengantisipasi perubahan yang diinginkan pada variabel pabrik dan menyediakan peralatan yang cukup ketika pabrik didesain. Desain peralatan yang tepat untuk kontrol harus dihitung berdasar perubahan yang diinginkan; yaitu dengan menambah kapasitas ekstra sekitar 20%, untuk ukuran peralatan yang tak tepat. Dalam beberapa kasus, ini akan menjadi sampah; di lain hal, kapasitas peralatan tidak akan tepat. Jika analisis ini tidak tepat atau perubahan di luar asumsi muncul, mencapai operasi pabrik
yang dapat diterima melalui manipulasi elemen kontrol final tidak memungkinkan.
1.5 bagaimana kontrol dilakukan?
Seperti yang kita lihat pada contoh mobil auto, feedback kontrol oleh aksi
manusia memungkinkan. Dalam beberapa hal, pendekatan ini layak, tapi untuk aksi perulangan kontinu melelahkan untuk orang. Sabagai tambahan, perhitungan beberapa kontrol cukup kompleks atau harus diimplementasikan terlalu cepat untuk dilakukan oleh orang. Oleh karena itu, kebanyakan feedback kontrol otomatis, dimana membutuhkan fungsi kunci dari sensing, kalkulasi, dan manipulasi dilakukan oleh peralatan dan tiap elemen berhubungan dengan elemen lain dalam sistem kontrol.
Sekarang, kebanyakan kontrol otomatis diimplementasikan menggunakan peralatan elektronik, dimana menggunakan tingkat arus listrik atau voltase untuk menggambarkan nilai untuk dikomunikasikan. Seperti yang diharapkan, banyak computing dan beberaap dari fungsi komunikasi ditampilkan secara meningkat biasanya denga teknologi digital. Dalam beberapa kasus, sistem kontrol menggunakan pneumatic, hidrolik, dan mekanisme mekanis untuk mengkalkulasi dan berkomunikasi; dalam sistem ini, sinyal digambarkan oleh tekanan atau posisi fisik.
Proses pabrik tipikal akan memiliki contoh untuk tiap instrumentasi dan komunikasi.
Sejak aspek penting dari proses kontrol ialah instrumentasi, buku ini
memperkenalkan beberapa sensor umum dan keran, tetapi pemilihan yang tepat dari peralatan ini untuk desain pabrik membutuhkan referensi untuk satu handbooks pada area ini sebagai tambahan.
Elemen kunci lainnya dari proses kendali ialah device (perangkat) melakukan perhitungan. Perhitungan kendali dilakukan oleh komputasi analog untuk sebagian besar sejarah dari process plant.
Peralatan komputasi analog diterapkan dengan membangun suatu system fisik. Pendekatan kalkulasi ini tidak fleksibel. Sebagai tambahan, kalkulasi yang kompleks tidak dapat dilakukan. Bagaimanapun juga beberapa control feed back masih diterapkan dengan alasan biaya dan reliabilitas yang sesuai dengan kondisi pabrik. Dengan kelebihan berupa computer digital yang berbiaya rendah, sebagian besar dari perhitungan control dan semua perhitungan kompleks dilakukan oleh computer digital. Sebagian besar dari prinsip-prinsip yang ada pada buku ini dapat diterapkan pada perangkat analog maupun digital.
Aspek-aspek tertentu dari control digital akan diperkenalkan pada Bab 11.
Pada semua Bab setelah Bab 11, prinsip-prinsip kendali dibahas beserta aspek-aspek tertentu dari baik penerapan analog maupun digital, maka kedua cara tersebut dalam melakukan kalkulasi akan dibahas pada suatu kesatuan.
Maka untuk pertanyaan “ Bagaimana kendali dilakukan?” jawabannya adalah sederhana yaitu “ secara otomatis menggunakan instrumentasi dan komputasi yang melakukan semua fitur dari control feedback tanpa adanya intervensi manusia.
1.6 Dimanakah kendali diimplementasikan ?
Secara fisik, pabrik-pabrik kimia besar dan kompleks. Orang-orang yang
bertanggung jawab untuk mengoperasikan pabrik dalam basis menit ke menit harus mempunyai informasi dari plant yang tersedia bagi mereka pada lokasi sentral.
Pengaturan yang paling umum dari peralatan control untuk mengakomodasi
kebutuhan ini ditunjukkan pada gambar (Figure) 1.6. Sewajarnya, sensor-sensor dan katup-katup terletak dalam proses. Sinyal-sinyal, yang biasanya elektronik, berkomunikasi dengan ruang kendali, dimana semua informasi ditampilkan untuk personil-personil operasional dan dimana kendali perhitungan dilakukan. Jarak antara proses dengan ruang kendali bervariasi dari beberapa ratus mil, bahkan lebih.
Pada suatu ruang kendali, suatu individu bertangggung jawab untuk
mengawasi dan mengoperasikan suatu bagian dari suatu pabrik yang kompleks dan besar, yang mengandung hingga 100 CV (controlled variables) dan 400 MV (measured variables) lainnya. Secara umum, plant tidak pernah beroperasi pada keadaan ‘automatic pilot’, selalu terdapat pekerja melakukan tugas-tugas ayng tidak seara otomatis, dengan tujuan mengoptimisasi operasi, dan untuk mengintervensi apabila suatu saat terjadi kejadian yang tidak biasa ataupun berbahaya, seperti kegagalan beroperasinya suatu peralatan. Pekerja lain yang ada pada peralatan proses,. Biasanya disebut sebagai pekerja yang berada di lapangan, untuk mengawasi peralatan dan untuk melakukan fungsi yang membutuhkan intervensi manual, sehingga pabrik kimia yang terautomisasi dengan baik, akan melibatkan interaksi antara perhitungan manusia dan perhitungan kontrol.
Konfigurasi kontrol lainnya adalah mungkin dan digunakan bila diperlukan.
Sebagai contoh, panel-panel kecil dengan instrumentasi yang dapat diletakkan didekat peralatan kritis dari suatu peralatan proses ketika operator membutuhkan suatu akses pada sistim kontrol selagi melakukan process adjustments pengaturan ini tidak akan mencegah sisa dari plant lainnya untuk dikontrol dari fasilitas sentral. Juga, banyak sensor-sensor yang menyediakan display visual dari suatu harga yang diukur, yang
dapat dilihat dari operator lokal sebagaimana suatu sinyal ditransmisikan pada ruang kendali pusat (sentral). Sehingga, operator lokal dapat menentukan kondisi operasi dari suatu unit, tetapi display lokal individual didistribusikan pada plant, tidak dikumpulkan pada satu tempat untuk operator lokal.
Jawaban singkat untuk pertanyaan lokasi adalah :
1. Sensor, indikator lokal, dan katup yang terdapat dalam proses
2. Display dari semua variabel plant dan kalkulasi kendali terdapat di fasilitas yang terpusat.
Peningkatan penggunaan dari komputasi digital tidak akan membuat distribusi dari kalkulasi kendali untuk lokasi sensor lebih praktis, tetapi untuk tujuan materi dari buku ini, semua kontroler akan dihubungkan pada suatu jaringan komputasi yang akan berfungsi seperti satu komputer.
1.7. Apakah insinyur teknik pengendalian (engineer of control engineering) itu?
Apa yang dapat dilakukan insinyur sehingga suatu plant dapat dipelihara reliabilitas dan keselamatannya hingga mendekati parameter yang diinginkan ? Sebagian besar keputusan dari insinyur tersebut akan dibahas pada lima topik berikut ini.
Desain proses
Kunci dalam teknik adalah desain dari sebuah proses sehingga proses dapat dikontrol degan baik. Misalnya pada pemanas ruangan terdapat temperatur maksimal dan minimal karena furnace dan heat exchanger tidak dapat merespon dengan cepat. Dengan begitu, sebuah plant yang lebih responsif akan dengan lebih mudah dikontrol. Responsif berarti variabel yang dikontrol dapat merespon dengan cepat untuk berapapun harga variabel yang dimanipulasi di-set. Dan juga, sebuah plant yang mudah beradaptasi dengan gangguan juga akan lebih mudah dikontrol.
Pengukuran
Kunci keputusan yang akan diambil adalah pemilihan jenis sensor dan
lokasinya, karena kita hanya dapat mengontrol nilai-nilai yang terukur.
Seorang insinyur harus memilih sensor yang dapat mengukur variabel-variabel penting dengan cepat dan dengan akurat.
Elemen akhir
Insinyur harus menyediakan alat, variabel yang dimanipulasi yang dapat
bersikap sesuai perhitungan kontrol. Contoh: contol valve sebagai elemen
akhir akan membuka atau menutup dengan persentasi bukaan/tutupan tertentu sesuai dengan signal yang dikirimkan ke valve dari kontroller.
Struktur kontrol
Insinyur harus dapat memutuskan beberapa hal paling dasar dalam
perancangan sistem kontrol. Misalnya, valve mana yang harus dimanipulasi
untuk mengontrol suatu pengukuran.
Perhitungan kontrol
Setelah struktur kontrol dan variabel sudah terpilih, persamaan-persamaan
tertentu harus dipilih untuk pengukuran nilai-nilai yang diinginkan untuk
menghitung variabel yang dimanipulasi. Seperti yang kita pelajari, hanya
beberapa persamaan yang sesuai untuk kontrol bagi berbagai macam plant.
1.8. Bagaimana kontrol proses didokumentasikan?
Ada banyak format untuk mendokumentasikan hasil. Yang paling umum
adalah spesifikasi dan ukuran alat, operasi manual, dan dokumentasi teknik dari eksperimen plant dan persamaan kontrol. Sebagai tambahan, insinyur kontrol memperluasnya dengan menggunakan gambar yang mempersentasikan berbagai perancangan tindakan. Penggambaran ini digunakan untuk berbagai tujuan, antara lain perancangan plant, pembelian alat dan evaluasi ulang prosedur keamanan dan operasi.
Untuk menghindari ketidaksepahaman maka dibuat standar simbol oleh “InstrumentSociety of America” yang digunakan di seluruh dunia. Contoh:
A Analyzer
F Laju alir
L Tinggi liquid dan solid dalam tangki
P Tekanan
T Suhu
Komunikasi ke sensor ditunjukkan sebagai garis utuh. Jika signal digunakan
hanya sebagai display bagi operator, mak ditambah simbol ‘I’ untuk indikator. Jika signal digunakan dalam perhitungan, maka ditunjukkan pula dalam sebuah lingkaran. Untuk kontroller, komunikasi ke elemen akhir ditunjukkan oleh garis putus-putus.
Simbol dasar dengan artinya terdapat di Appendix A. Versi simple dari
Standar Persatuan instrument Amerika cukup sudah cukup untuk buku ini dan akan menyediakan latar belakang yang cukup untuk penggambaran yang lebih rumit. Walaupun menggunakan standar merupakan kerja tambahan pada awalnya. Ini harus dipertimbangkan sebagai investasi kecil yang mengarah ke komunikasi yang benar, seperti belajar grammar dan vocabulary, digunakan oleh seluruh insinyur teknik kimia.
1.9. Sample apa yang mengontrol strategi?
Contoh sederhana system proses control diberikan pada gambar 1.7a sampai d. masing-masing gambar mencakup skema proses, sebuah kontroler (di aliran instrumentasi), serta hubungan antara variabel terukur dan manipulasi. Sebagai latihan pikiran, anda bisa menganalisa masing-masing system proses control untuk membuktikan hubungan sebab-akibat pada proses dan untuk mengetahui aksi dari kontroler yang akan diambil sebagai respon dari gangguan atau perubahan suatu nilai (set point).
Sebagai contoh, pada gambar 1.7a, dengan kenaikan temperature inlet,
system control akan melakukan peningkatan komposisi outlet dari reaktan.
Denganrespon, system control akan mengatur katup koil pemanas, menutupnya perlahan, sampai komposisi akhi sesuai dengan nilai yang diinginkan.
Contoh dari proses diagram yang lebih rumit, tanpa disain control, diberika
pada fig.1.8. Prosesnya mencakup reactor kimia, flash separator, heat exchanger dan aliran perpaan yang menghubungi. Catat bahwa sebuah insinyur disain control harus memilih pengukuran dan katup yang mungkin untuk mengetahui hubungan kontroler dari sekian banyak kemungkinan. Di chapter 25 anda akan mendisain system control untuk proses ini yang mengontrol variable kunci, seperti level reactor dan temperature separator, berdasarkan pada tujuan control
1.10. Kesimpulan
Materi chapter ini mengenai pengenalan kualitatif proses control. Anda telah belajarciri-ciri kunci dari feedback control begitu juga dengan tipe dari peralatan (instrument dan computer) yang dibutuhkan proses control ini. Pentingnya disain proses pada pengontrolan beberapa kali dibahas pada capter ini.
Berdasarkan pada pengenalan ini, kita dipersiapkan untuk membahas secara lebih hati-hati tujuan akhir dari proses control di chapter 2. Pengetahuan tentang tujuan akhir proses control penting untuk pemilihan tipe analisis yang digunakan di teknik control.
Disadur dari
http://www.chemeng.ui.ac.id/~wahid/kendali/Bab 1 Pengantar Pengendalian Proses.pdf
Terma kasih Pak Ir. Abdul Wahid, MT.
"Tjetjep"
1.1. PENDAHULUAN
Ketika kita melakukan pengamatan pada proses kimia di pabrik atau
laboratorium, maka terdapat banyak aliran dari vessel ke vessel, gelembung cairan dan material viscous serta semua alat berubah secara terus menerus. Dengan perubahan sedikit saja maka bisa terdapat respon yang berakibat fatal. Kesimpulan dari wacana sementara ini adalah bahwa dunia adalah sebuah dinamika dan ini merupakan alasan yang tepat untuk adanya sebuah proses kontrol. Dalam memahami perilaku sistem maka seorang engineer process design dapat memahami prilaku dinamiknya.
Teknik pengontrolan adalah ilmu teknik yang digunakan pada banyak aplikasi misalnya kimia, listrik dan teknik mesin serta diterapkan pada berbagai sistem fisik mulai dari sirkuit elektrik sampai pada perancangan robot. Dalam bidang ilmu teknik kimia proses kontrol diterapkan pada disain reaktor, Heat exchanger, dan peralatan transfer massa lainnya.
Proses kontrol adalah topik esensial bagi seorang chemical engineers misalnya pada perancangan pabrik yang harus mempertimbangkan prilaku dinamik pada semua peralatan karena pabrik tidak beroperasi secara steady state.
Engineers yang bertanggung jawab pada beroperasinya pabrik harus
memastika bahwa respon yang terjadi akibat adanya gangguan harus bsa diatasi agar tetap aman dan menguntungkan.
Kesimpulannya tugas seorang engineers untuk mendisain, membangun dan
mengoperasikan sistem fisik adalah sebuah aktivitas untuk menjaga sistem pada kondisi yang diinginkan.
Teknik proses kontrol meliputi analisis matematika dan praktek teknik,
sebelum kita memahami tujuan dari prinsip proses kontrol dan perhitungannya maka kita harus mengetahui tujuan dari proses kontrol dan hubungannya dengan teknik kimia. Bab ini akan membahas mengenai pertanyaan- pertanyaan sebagai berikut :
Ø Apa saja yang dilakukan proses kontrol?
Ø Mengapa diperlukan proses kontrol?
Ø Mengapa dimngkinkan adanya proses kontrol?
Ø Bagaimana proses kontrol dilakukan?
Ø Dimana sistem kontrol diterapkan?
Ø Apa saja yang dilakukan control engineer?
Ø Bagaimana proses kontrol didokumentasikan?
Ø Apa saja contoh dari sistem kontrol yang strategis?
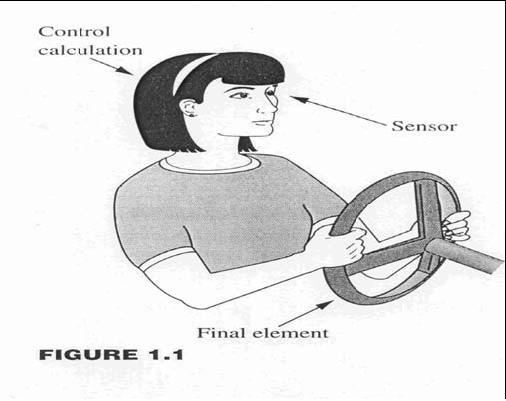
1.2. Apa saja yang dilakukan oleh proses kontrol ?
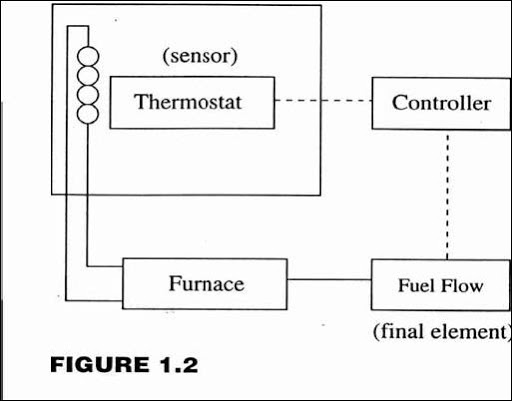
Pertama tama kita akan mendiskusikan mengenai 2 contoh dari sistem kontrol yang terdapat dalam kehidupan kita sehari-hari kemudian kita akan mendiskusikan mengenai sistem yang lebih umum dalam defenisi sistem kontrol dan feedback kontrol.
Contoh pertama adalah orang yang mengendarai mobil seperti yang ditunjukan oleh Gambar 1.1. Supir harus memiliki tujuan atau objektif. Pertama tama supir harus menentukan lokasi dari mobil di jalan dengan menggunkan mata untuk melihat posisi mobil di jalan kemudian supir juga harus memperhitungkan keaadan agar menjaga mobil tetap pada posisi yang diinginkan di jalan dan akhirnya supir haruslah mengubah posisi mobil dengan menggunakan stir. Dengan mengunakan ketiga cara ini maka supir bisa menjaga mobil tetap berada pada posisi ynang diinginkan.
Contoh kedua adalah sistem pemanas sederhana seperti yang ditunjukan
gambar 1.2. Rumah yang berada pada daerah beriklim dingin bisa menaikan suhu dengan menggunakan pemanas. Temperatur dalam ruangan diukur oleh termostat yang kemudian membandingkannya dengan temperatur ruang pada range yang diinginkan, katakanlah 18 sampai 22oC. Jika temperature dibawah 18oC, furnace dan pompa akan menyala, dan jika temperature di atas 22oC, furnace dan pompa akan berhenti bekerja. Jika temperature diantara 18 sampai 22oC,kondisi furnace dan pompa tidak akan berubah. Secara umum prilaku dari kondisi temperature dalam rumah diberikan dalam figure 1.3, yang menunjukkan bagaimana temperature
bergeser secara perlahan dari batas atas dan bawah. Dapat dilihat juga bahwa ada suatu saat prilaku temperature melewati batas-batas tersebut, karena furnace dan heat exchanger tidak memberikan respons secepatnya. Pendekatan ini dinamakan “on/off”control dan dapat digunakan sewaktu control yang akurat pada nilai yang diinginkan tidak diperlukan. Kita akan membahas metode pengontrolan yang lebih baik di bagian berikutnya, dimana dapat mempertahankan variable yang penting cukup dekat pada nilai yang diinginkan.
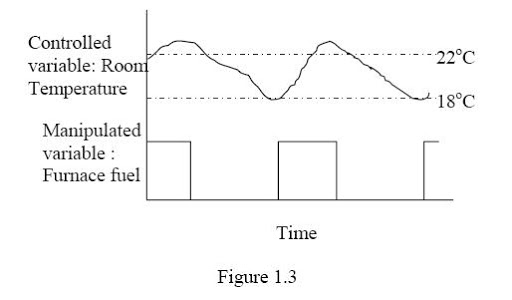
Setelah tadi kita membahas secara sekilas mengenai dua sistem control,
kemudian kita akan mengidentifikasikan beberapa fitur umum. Yang pertama adalah tiap sistem menggunakan nilai yang spesifik (atau range) sebagai nilai yang diinginkan sebagai variable yang dikontrol. Sewaktu kita membahas kalkulasi control dalam Bagian III, kita akan menggunakan istilah set point untuk nilai yang diinginkan. Yang kedua, Kondisi dari sistem diukur; yakni semua sistem control menggunakan sensor untuk mengukur variable fisis yang akan dijaga dekat dengan nilai yang diinginkan. Yang ketiga, tiap sistem mempunyai kalkulasi control, atau
algoritma, dimana menggunakan hasil pengukuran dan nilai yang diinginkan untuk menentukan koreksi pada proses operasi. Kalkulasi control untuk pemanas ruangan adalah contoh yang sangat sederhana (on/off), sedangkan control yang digunakan pada contoh “si pengemudi” akan sangat kompleks. Akhirnya, hasil kalkulasi akan diimplentasikan dengan mengeset salah satu alat pada sistem, dimana istilahnya adalah final control element, seperti setir mobil atau tombol saklar furnace dan pompa. Kunci fitur tersebut ditunjukkan secara skematik pada figure 1.4, dimana
dapat digunakan untuk merepresentasikan banyak sistem control.
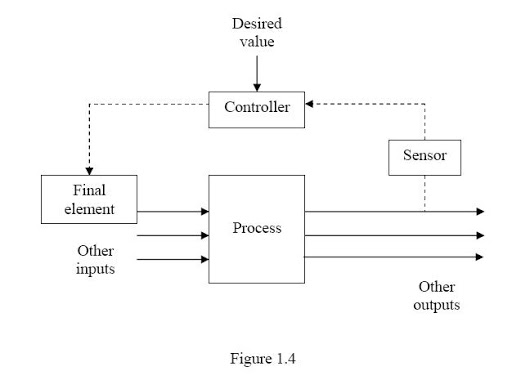
Setelah tadi kita membahas beberapa sistem control umum dan mengidentifikasikan kunci fitur, sekarang kita akan mendefinisikan istilah control. Kamus meberikan definisi untuk kata control sebagai “untuk mempengaruhi secara langsung”. Kita akan menggunakan definisi yang mirip dalam penerapan keperluan kita. Definisi berikut ini cocok untuk dua contoh fisis dan representasi skematik pada figure 1.4.
Control(verb): untuk mempertahankan kondisi yang diinginkan dalam sistem fisis dengan mengatur variable tertentu dalam sistem.
Contoh control mempunyai fitur tambahan yang amat penting. Itu adalah
feedback, yang didefinisikan sebagai berikut:
Feedback control menggunakan hasil keluaran output dari sistem untuk
mempengaruhi input dari sistem yang sama.
Sebagai contoh, temperatur ruangan yang digunakan, melewati keputusan
on/off thermostat, untuk mempengaruhi aliran air panas menuju heat exchanger. Sewaktu feedback digunakan untuk mengurangi perbedaan antara nilai aktual dan nilai yang diinginkan, ini dinamakan dengan “negative feedback”. Kecuali dinyatakan lain, maka kita selalu mendiskusikan negative feedback dan tidak akan menggunakan kata ‘negatif’. Dalam ilmu sosial dan vernacular umum, frasa “negative feedback” mengindikasikan perubahan yang tidak diinginkan, karena sebagian besar orang tidak menikmati menerima sinyal yang menyatakan mereka untuk mengoreksi kesalahan. Sebagian besar orang lebih suka menerima “positive feedback”, sinyal yang menyatakan mereka untuk melanjutkan kecenderungan untuk mencapai kondisi yang diinginkan. Perbedaan dalam terminologi ini sangat disayangkan; kita akan menggunakan terminologi pada kontrol otomatis, dimana “negatif” mengindikasikan perubahan yang bertujuan untuk mencapai nilai yang diinginkan diseluruh isi buku ini, tanpa kecuali.
Kegunaan penting dari feedback pada sistem kontrol dapat dilihat dengan
menganggap suatu alternatif tanpa feedback. Sebagai contoh, pendekatan alternatif dari pengaturan suhu ruangan yang diinginkan akan dilakukan dengan mengeset aliran air panas berdasarkan pengukuran temperatur luar ruangan dan model untuk kehilangan panas dari dalam ruangan. (tipe alternatif ini dinamakan feedforward, akan dibahas belakangan di buku ini, dimana penggunaannya bersamaan dengan feedback akan dibahas). Strategi tanpa feedback untuk mempertahankan suhu ruangan takkan
berhasil bila model tersebut mempunyai error—seperti yang biasanya terjadi. Beberapa penyebab dari error bisa disebabkan oleh kecepatan angin dan alian udara dari jendela yang terbuka. Di lain pihak, feedback dapat selalu memanipulasi final element untuk mencapai nilai yang diinginkan. Oleh karena itu, feedback menyediakan fitur yang kuat agar sistem kontrol dapat mencapai nilai terukur dekat dengan nilai yang diinginkan tanpa memerlukan model plant secara tepat.
Sebelum kita menyelesaikan bagian ini, istilah input dan output harus
diklarifikasikan. Sewaktu digunakan dalam pembahasan sistem kontrol, input dan output tidak ditujukan untuk material yang bergerak masuk dan keluar sistem. Disini istilah input ditujukan untuk variabel yang menyebabkan output. Dalam contoh ‘mengemudi’ input adalah posisi setir dan output adalah posisi mobil. Pada contoh pemanas ruangan, input adalah bahan bakar untuk furnace dan output adalah temperatur ruangan. Sangat penting untuk diketahui bahwa input menyebabkan output dan hubungan ini tidak dapat dibalik. Hubungan sebab-akibat yang timbul pada proses fisis memaksa kita untuk memilih input sebagai variabel manipulasi dan output sebagai variabel terukur. Banyak contoh dengan seleksi dari variabel kontrol dan variabel manipulasi akan ditampilkan dalam chapter berikut.
Oleh karena itu, jawaban untuk pertanyaan pertama mengenai fungsi kontrol adalah,” sistem kontrol feedback mempertahankan variabel spesifik dekat dengan nilai yang diinginkan dengan mengaplikasikan empat fitur dasar ditunjukkan dalam figur1.4.” Memahami dan mendesain sistem kontrol feedback merupakan tujuan utama dari buku ini.
1.3 Kenapa kontrol diperlukan?
Sebuah pertanyaan alami kedua terlibat kebutuhan akan kontrol. Ada dua
alasan utama untuk kontrol, dimana akan didiskusikan dengan respek untuk tangki berpengaduk yang sederhana dengan penukar panas yang digambarkan pada gambar1.5. Fluida proses mengalir ke dalam tangki dari sebuah pipa dan mengalir keluar dari tangki oleh aliran berlebih. Oleh karena itu, volume tangki konstan. Fluida pemanas mengalir dapat diatur dengan mengubah bukaan keran pada media aliran pemanas. Suhu dalam tangki dapat dikontrol.
Alasan pertama kontrol ialah untuk mempertahankan suhu pada nilai yang
diinginkan ketika gangguan muncul. Beberapa ganggguan khas untuk proses ini terjadi pada variabel berikut: laju alir dan suhu fluida proses masukan, suhu fluida pemanas dan tekanan aliran pemanas upstream dari keran. Sebagai latihan, anda sebaiknya menentukan bagaimana keran harus diatur (dibuka dan ditutup) pada respon utnuk meningkatkan pada tiap-tiap varibel gangguan tersebut.
Alasan kedua kontrol ialah untuk merespon perubahan pada nilai yang
diinginkan. Sebagai contoh, jika suhu yang diinginkan pada tangki berpengaduk dengan penukar panas ditingkatkan, persentase keran pemanas harus ditingkatkan. Nilai yang diinginkan berdasar pada analisis operasi pabrik dan sasaran. Analisis ini akan didiskusikan dalam bab 2, dimana topik utama diatur dalam tujuh kategori:
1. keselamatan
2. perlindungan lingkungan
3. perlindungan peralatan
4. operasi pabrik yang mulus dan laju produksi
5. kualitas produk
6. optimalisasi laba
7. pengawasan dan diagnosis
Topik ini ditranslasikan pada nilai variabel – suhu, tekanan, aliran, dan selanjutnya – dimana dapat dikontrol.
1.4 kenapa kontrol memungkinkan?
Desain yang tepat dari peralatan pabrik sangat penting untuk kontrol yang
memungkinkan dan untuk kontrol memberikan kinerja dinamik yang baik. Oleh karena itu, kontrol dan operasi dinamis merupakan faktor yang sangat penting pada desain pabrik. Berdasar pada fitur kunci dari kontrol umpan balik pada gambar1.4, desain pabrik harus termasuk sensor yang cukup dari variabel keluaran pabrik dan elemen kontrol final. Sensor harus merespon secara cepat sehingga aksi kontrol dapat diambil dalam waktu nyata. Sensor menggunakan variasi prinsip fisik yang ada untuk variabel proses dasar (aliran, suhu, tekanan, dan level), komposisi (seperti fraksi mol)
dan sifat fisik (densitas, viskositas, kalor pembakaran). Banyak sensor disertakan pada peralatan proses, dengan sebuah pelapis melindungi mereka dari efek korosi dari aliran. Yang lain membutuhkan sampel diambil secara periodik dari proses; sebagai catatan sampling ini dapat secara otomatis sehingga hasil sensor baru ada untuk interval frekuensi. Elemen kontrol final dari proses kimia biasanya berupa keran mempengaruhi aliran fluida, tetapi mereka dapat merupakan variabel manipulasi lainnya, seperti tenaga untuk motor elektrik atau kecepatan pada sabuk pemutar.
Pemikiran penting lainnya ialah kapasitas dari peralatan proses. Peralatan
harus mempunyai kapasitas yang cukup besar untuk merespon semua gangguan yang diharapkan dan perubahan pada nilai yang diinginkan. Untuk tangki berpengaduk dengan penukar panas, tugas maksimum, yang dipengaruhi oleh suhu, area dan laju alir media pemanas, harus cukup besar untuk mempertahankan suhu tangki untuk mengantisipasi semua gangguan. Tugas yang paling besar berhubungan dengan suhu keluaran maksimum, aliran fluida maksimum, suhu fluida masukan terendah, dan
kehilangan kalor maksimum ke lingkungan. Setiap proses harus dianalisa untuk meyakinkan kapasitas yang tepat. Diskusi lebih lanjut dari topik ini muncul pada dua bab selanjutnya.
Alhasil, sebagai jawaban kenapa kontrol memungkinkan ialah kita mengantisipasi perubahan yang diinginkan pada variabel pabrik dan menyediakan peralatan yang cukup ketika pabrik didesain. Desain peralatan yang tepat untuk kontrol harus dihitung berdasar perubahan yang diinginkan; yaitu dengan menambah kapasitas ekstra sekitar 20%, untuk ukuran peralatan yang tak tepat. Dalam beberapa kasus, ini akan menjadi sampah; di lain hal, kapasitas peralatan tidak akan tepat. Jika analisis ini tidak tepat atau perubahan di luar asumsi muncul, mencapai operasi pabrik
yang dapat diterima melalui manipulasi elemen kontrol final tidak memungkinkan.
1.5 bagaimana kontrol dilakukan?
Seperti yang kita lihat pada contoh mobil auto, feedback kontrol oleh aksi
manusia memungkinkan. Dalam beberapa hal, pendekatan ini layak, tapi untuk aksi perulangan kontinu melelahkan untuk orang. Sabagai tambahan, perhitungan beberapa kontrol cukup kompleks atau harus diimplementasikan terlalu cepat untuk dilakukan oleh orang. Oleh karena itu, kebanyakan feedback kontrol otomatis, dimana membutuhkan fungsi kunci dari sensing, kalkulasi, dan manipulasi dilakukan oleh peralatan dan tiap elemen berhubungan dengan elemen lain dalam sistem kontrol.
Sekarang, kebanyakan kontrol otomatis diimplementasikan menggunakan peralatan elektronik, dimana menggunakan tingkat arus listrik atau voltase untuk menggambarkan nilai untuk dikomunikasikan. Seperti yang diharapkan, banyak computing dan beberaap dari fungsi komunikasi ditampilkan secara meningkat biasanya denga teknologi digital. Dalam beberapa kasus, sistem kontrol menggunakan pneumatic, hidrolik, dan mekanisme mekanis untuk mengkalkulasi dan berkomunikasi; dalam sistem ini, sinyal digambarkan oleh tekanan atau posisi fisik.
Proses pabrik tipikal akan memiliki contoh untuk tiap instrumentasi dan komunikasi.
Sejak aspek penting dari proses kontrol ialah instrumentasi, buku ini
memperkenalkan beberapa sensor umum dan keran, tetapi pemilihan yang tepat dari peralatan ini untuk desain pabrik membutuhkan referensi untuk satu handbooks pada area ini sebagai tambahan.
Elemen kunci lainnya dari proses kendali ialah device (perangkat) melakukan perhitungan. Perhitungan kendali dilakukan oleh komputasi analog untuk sebagian besar sejarah dari process plant.
Peralatan komputasi analog diterapkan dengan membangun suatu system fisik. Pendekatan kalkulasi ini tidak fleksibel. Sebagai tambahan, kalkulasi yang kompleks tidak dapat dilakukan. Bagaimanapun juga beberapa control feed back masih diterapkan dengan alasan biaya dan reliabilitas yang sesuai dengan kondisi pabrik. Dengan kelebihan berupa computer digital yang berbiaya rendah, sebagian besar dari perhitungan control dan semua perhitungan kompleks dilakukan oleh computer digital. Sebagian besar dari prinsip-prinsip yang ada pada buku ini dapat diterapkan pada perangkat analog maupun digital.
Aspek-aspek tertentu dari control digital akan diperkenalkan pada Bab 11.
Pada semua Bab setelah Bab 11, prinsip-prinsip kendali dibahas beserta aspek-aspek tertentu dari baik penerapan analog maupun digital, maka kedua cara tersebut dalam melakukan kalkulasi akan dibahas pada suatu kesatuan.
Maka untuk pertanyaan “ Bagaimana kendali dilakukan?” jawabannya adalah sederhana yaitu “ secara otomatis menggunakan instrumentasi dan komputasi yang melakukan semua fitur dari control feedback tanpa adanya intervensi manusia.
1.6 Dimanakah kendali diimplementasikan ?
Secara fisik, pabrik-pabrik kimia besar dan kompleks. Orang-orang yang
bertanggung jawab untuk mengoperasikan pabrik dalam basis menit ke menit harus mempunyai informasi dari plant yang tersedia bagi mereka pada lokasi sentral.
Pengaturan yang paling umum dari peralatan control untuk mengakomodasi
kebutuhan ini ditunjukkan pada gambar (Figure) 1.6. Sewajarnya, sensor-sensor dan katup-katup terletak dalam proses. Sinyal-sinyal, yang biasanya elektronik, berkomunikasi dengan ruang kendali, dimana semua informasi ditampilkan untuk personil-personil operasional dan dimana kendali perhitungan dilakukan. Jarak antara proses dengan ruang kendali bervariasi dari beberapa ratus mil, bahkan lebih.
Pada suatu ruang kendali, suatu individu bertangggung jawab untuk
mengawasi dan mengoperasikan suatu bagian dari suatu pabrik yang kompleks dan besar, yang mengandung hingga 100 CV (controlled variables) dan 400 MV (measured variables) lainnya. Secara umum, plant tidak pernah beroperasi pada keadaan ‘automatic pilot’, selalu terdapat pekerja melakukan tugas-tugas ayng tidak seara otomatis, dengan tujuan mengoptimisasi operasi, dan untuk mengintervensi apabila suatu saat terjadi kejadian yang tidak biasa ataupun berbahaya, seperti kegagalan beroperasinya suatu peralatan. Pekerja lain yang ada pada peralatan proses,. Biasanya disebut sebagai pekerja yang berada di lapangan, untuk mengawasi peralatan dan untuk melakukan fungsi yang membutuhkan intervensi manual, sehingga pabrik kimia yang terautomisasi dengan baik, akan melibatkan interaksi antara perhitungan manusia dan perhitungan kontrol.
Konfigurasi kontrol lainnya adalah mungkin dan digunakan bila diperlukan.
Sebagai contoh, panel-panel kecil dengan instrumentasi yang dapat diletakkan didekat peralatan kritis dari suatu peralatan proses ketika operator membutuhkan suatu akses pada sistim kontrol selagi melakukan process adjustments pengaturan ini tidak akan mencegah sisa dari plant lainnya untuk dikontrol dari fasilitas sentral. Juga, banyak sensor-sensor yang menyediakan display visual dari suatu harga yang diukur, yang
dapat dilihat dari operator lokal sebagaimana suatu sinyal ditransmisikan pada ruang kendali pusat (sentral). Sehingga, operator lokal dapat menentukan kondisi operasi dari suatu unit, tetapi display lokal individual didistribusikan pada plant, tidak dikumpulkan pada satu tempat untuk operator lokal.
Jawaban singkat untuk pertanyaan lokasi adalah :
1. Sensor, indikator lokal, dan katup yang terdapat dalam proses
2. Display dari semua variabel plant dan kalkulasi kendali terdapat di fasilitas yang terpusat.
Peningkatan penggunaan dari komputasi digital tidak akan membuat distribusi dari kalkulasi kendali untuk lokasi sensor lebih praktis, tetapi untuk tujuan materi dari buku ini, semua kontroler akan dihubungkan pada suatu jaringan komputasi yang akan berfungsi seperti satu komputer.
1.7. Apakah insinyur teknik pengendalian (engineer of control engineering) itu?
Apa yang dapat dilakukan insinyur sehingga suatu plant dapat dipelihara reliabilitas dan keselamatannya hingga mendekati parameter yang diinginkan ? Sebagian besar keputusan dari insinyur tersebut akan dibahas pada lima topik berikut ini.
Desain proses
Kunci dalam teknik adalah desain dari sebuah proses sehingga proses dapat dikontrol degan baik. Misalnya pada pemanas ruangan terdapat temperatur maksimal dan minimal karena furnace dan heat exchanger tidak dapat merespon dengan cepat. Dengan begitu, sebuah plant yang lebih responsif akan dengan lebih mudah dikontrol. Responsif berarti variabel yang dikontrol dapat merespon dengan cepat untuk berapapun harga variabel yang dimanipulasi di-set. Dan juga, sebuah plant yang mudah beradaptasi dengan gangguan juga akan lebih mudah dikontrol.
Pengukuran
Kunci keputusan yang akan diambil adalah pemilihan jenis sensor dan
lokasinya, karena kita hanya dapat mengontrol nilai-nilai yang terukur.
Seorang insinyur harus memilih sensor yang dapat mengukur variabel-variabel penting dengan cepat dan dengan akurat.
Elemen akhir
Insinyur harus menyediakan alat, variabel yang dimanipulasi yang dapat
bersikap sesuai perhitungan kontrol. Contoh: contol valve sebagai elemen
akhir akan membuka atau menutup dengan persentasi bukaan/tutupan tertentu sesuai dengan signal yang dikirimkan ke valve dari kontroller.
Struktur kontrol
Insinyur harus dapat memutuskan beberapa hal paling dasar dalam
perancangan sistem kontrol. Misalnya, valve mana yang harus dimanipulasi
untuk mengontrol suatu pengukuran.
Perhitungan kontrol
Setelah struktur kontrol dan variabel sudah terpilih, persamaan-persamaan
tertentu harus dipilih untuk pengukuran nilai-nilai yang diinginkan untuk
menghitung variabel yang dimanipulasi. Seperti yang kita pelajari, hanya
beberapa persamaan yang sesuai untuk kontrol bagi berbagai macam plant.
1.8. Bagaimana kontrol proses didokumentasikan?
Ada banyak format untuk mendokumentasikan hasil. Yang paling umum
adalah spesifikasi dan ukuran alat, operasi manual, dan dokumentasi teknik dari eksperimen plant dan persamaan kontrol. Sebagai tambahan, insinyur kontrol memperluasnya dengan menggunakan gambar yang mempersentasikan berbagai perancangan tindakan. Penggambaran ini digunakan untuk berbagai tujuan, antara lain perancangan plant, pembelian alat dan evaluasi ulang prosedur keamanan dan operasi.
Untuk menghindari ketidaksepahaman maka dibuat standar simbol oleh “InstrumentSociety of America” yang digunakan di seluruh dunia. Contoh:
A Analyzer
F Laju alir
L Tinggi liquid dan solid dalam tangki
P Tekanan
T Suhu
Komunikasi ke sensor ditunjukkan sebagai garis utuh. Jika signal digunakan
hanya sebagai display bagi operator, mak ditambah simbol ‘I’ untuk indikator. Jika signal digunakan dalam perhitungan, maka ditunjukkan pula dalam sebuah lingkaran. Untuk kontroller, komunikasi ke elemen akhir ditunjukkan oleh garis putus-putus.
Simbol dasar dengan artinya terdapat di Appendix A. Versi simple dari
Standar Persatuan instrument Amerika cukup sudah cukup untuk buku ini dan akan menyediakan latar belakang yang cukup untuk penggambaran yang lebih rumit. Walaupun menggunakan standar merupakan kerja tambahan pada awalnya. Ini harus dipertimbangkan sebagai investasi kecil yang mengarah ke komunikasi yang benar, seperti belajar grammar dan vocabulary, digunakan oleh seluruh insinyur teknik kimia.
1.9. Sample apa yang mengontrol strategi?
Contoh sederhana system proses control diberikan pada gambar 1.7a sampai d. masing-masing gambar mencakup skema proses, sebuah kontroler (di aliran instrumentasi), serta hubungan antara variabel terukur dan manipulasi. Sebagai latihan pikiran, anda bisa menganalisa masing-masing system proses control untuk membuktikan hubungan sebab-akibat pada proses dan untuk mengetahui aksi dari kontroler yang akan diambil sebagai respon dari gangguan atau perubahan suatu nilai (set point).
Sebagai contoh, pada gambar 1.7a, dengan kenaikan temperature inlet,
system control akan melakukan peningkatan komposisi outlet dari reaktan.
Denganrespon, system control akan mengatur katup koil pemanas, menutupnya perlahan, sampai komposisi akhi sesuai dengan nilai yang diinginkan.
Contoh dari proses diagram yang lebih rumit, tanpa disain control, diberika
pada fig.1.8. Prosesnya mencakup reactor kimia, flash separator, heat exchanger dan aliran perpaan yang menghubungi. Catat bahwa sebuah insinyur disain control harus memilih pengukuran dan katup yang mungkin untuk mengetahui hubungan kontroler dari sekian banyak kemungkinan. Di chapter 25 anda akan mendisain system control untuk proses ini yang mengontrol variable kunci, seperti level reactor dan temperature separator, berdasarkan pada tujuan control
1.10. Kesimpulan
Materi chapter ini mengenai pengenalan kualitatif proses control. Anda telah belajarciri-ciri kunci dari feedback control begitu juga dengan tipe dari peralatan (instrument dan computer) yang dibutuhkan proses control ini. Pentingnya disain proses pada pengontrolan beberapa kali dibahas pada capter ini.
Berdasarkan pada pengenalan ini, kita dipersiapkan untuk membahas secara lebih hati-hati tujuan akhir dari proses control di chapter 2. Pengetahuan tentang tujuan akhir proses control penting untuk pemilihan tipe analisis yang digunakan di teknik control.
Disadur dari
http://www.chemeng.ui.ac.id/~wahid/kendali/Bab 1 Pengantar Pengendalian Proses.pdf
Terma kasih Pak Ir. Abdul Wahid, MT.
"Tjetjep"
Rabu, 23 Juli 2008
Aku dan Keluargaku
Langganan:
Postingan (Atom)